Experimental study of clinker grinding in a ball mill …
Experimental study of clinker grinding in a ball mill and the behavior of the grinding media inside the equipment using DEM. August 2022. Brazilian Journal of …
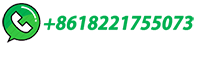
Experimental study of clinker grinding in a ball mill and the behavior of the grinding media inside the equipment using DEM. August 2022. Brazilian Journal of …
The cement ball mill is a kind of cement grinding mill.It is mainly used for grinding the clinker and raw materials of the cement plant, and also for grinding various ores in metallurgical, chemical, and electric power …
1. Optimization of the Cement Ball Mill Operation. Optimization addresses the grinding process, maintenance and product quality. The objective is to achieve a more efficient operation and increase the production rate as well as improve the run factor. Consistent quality and maximum output with lower specific power consumption results in lower ...
This paper presents results regarding the grinding behaviour of two batches of material (clinker) in a ball mill with its own two-step grinding process: the first one …
Batch dry grinding tests of cement clinker were performed in a ball mill measuring the power input. The effect of ball size distribution on specific selection functions was investigated. At the initial size reduction stage the experimental results show that the breakage process is more efficient with a maximal specific selection function.
The energy consumption of grinding is the subject of many studies, especially in the case of ball mills for grinding clinkers [8, 9], fuels [10], iron ore [11], hematite ore [12], sulfide ore [13 ...
The use of high-pressure grinding rolls (HPGR) prior to ball mills has become a common practice in cement clinker grinding due to significant energy savings in comparison to ball milling alone. The energy savings has been attributed to higher energy efficiency of HPGR at low reduction ratios, smaller particle top sizes in the ball mill feed, …
Attritor mills are versatile and efficient types of milling equipment used for grinding and mixing materials. They offer several advantages over other types of mills, including better grinding efficiency, precise control over particle size and distribution, and uniform mixing. If you are looking for a milling solution that can handle a wide ...
In this study, the milling of clinker was evaluated by varying the mill speed (24 and 72 RPM), residence time (3 and 5 hours) and grinding media load (30 and 40 %) in a ball mill.
Samples of the input, output and return material of cement clinker grinding by a CKP mill are collected, based on the field sampling in the industrial mill. The crushing kinetic process of the cement clinker in a CKP mill is analyzed, by using the particle size distribution and mass balances. The following results have been obtained. 1.
Chemical process industries are running under severe constraints, and it is essential to maintain the end-product quality under disturbances. Maintaining the product quality in the cement grinding process in the …
After exiting the cement kiln, the clinker is cooled and stored. To produce cement, clinker is mixed with a small amount of gypsum and other additives, such as pozzolans or slag. This mixture is then ground in the cement ball mill. The grinding process involves passing the clinker and additives through the rotating drum of the ball …
In the first sampling period HPGR feed clinker was ground in a laboratory ball mill to give approximately the same percentage of − 90 μm as compared to the industrial HPGR product for both sampling periods. Clinker as sampled from the plant was ground in a laboratory ball mill having a diameter of 700 mm and a length of 500 mm.
Cement ball mill in clinker grinding plan. Cement plants, on the other hand, are better suited for large-scale projects and can produce a full range of cement products. They are also better suited for more centralized locations, as the transportation of raw materials and finished products can be more efficient. However, the setup and …
Up to now, many laboratory-scale studies have been conducted with ball mill to examine the influences of the grinding aids on grinding performance. Sohoni et al. [14] investigated the influences of seven grinding aids on the batch grinding of limestone, Portland cement clinker and quartz.
Nowadays, ball mills are widely used in cement plants to grind clinker and gypsum to produce cement. The research focuses on the mill speed as well as air classifier speed effect on the two ...
A classic and robust design meant for all site locations, user friendly, low maintenance, less capital cost, easy availability of spares. Manufacturer of Ball Mill - Clinker Grinding Ball Mill, Cement Clinker Ball Mill, Shoe Slide Ball Mill and Ball Grinding Mill offered by Chanderpur Works Private Limited, Yamuna Nagar, Haryana.
To investigate the effects of grinding media shapes on the grinding kinetics of ball mill cement clinker, the grinding effects with ϕ20 mm balls and ϕ20 × 20 mm cylinders on six different size ...
The theoretical context of slope n of RRSB particle size distribution for the ball mill and the vertical roller mill was confirmed by investigations in the tkIS technical center. The vertical roller mill produces steeper particle size distribution than a ball mill [].Earlier determination of grindability according to ZEISEL for calcined clay and clinker …
... Figure 1 presents the design of the clinker grinding system (closed circuit), which consists of a two-chamber ball mill and the separator (Plasari and T heraska, 19 81). Cement...
Clinker grinding technology is the most energy-intensive process in cement manufacturing. Traditionally, it was treated as "low on technology" and "high on energy" as grinding circuits use more than 60 per cent of total energy consumed and account for most of the manufacturing cost. ... Ball mill grinding Evolution of ball mills was the ...
See more on cshub.mit.edu
WEBAs a general rule, there should be less than 25% of clinker that is below 1mm in size. Coarse clinker is more of an issue for ball mills. Some cement groups use a formula, …
In this paper, the method was used to study the collisions between grinding media and grinding media and walls in ball mills, which is the most used unit operation in clinker …
Cement additives. permit to reach both the targets. Grinding aids reduce particle. re -agglomeration during and after the milling process, improving. its yield. Strength enhancers push clinker ...
The use of high-pressure grinding rolls (HPGR) prior to ball mills has become a common practice in cement clinker grinding due to significant energy savings in comparison to ball milling alone.
Based on the above considerations for crushing and grinding, the energy consumption for the clinker pre-crushing and ball milling can be estimated using the following Bond based model: (9) W = W c + W m As pre-crushing product size P c is equal to the mill feed size F 80 then: (10) W = A F 80 W i 10 P 80-10 F c + 1.3 ∗ 2.44 D 0.2 ∗ R …
A radiotracer investigation was carried out in a ball mill of a cement plant in Kenya. Residence time distribution (RTD) of raw feed to the mill was measured using Technetium-99m adsorbed on the ...
The 2.4x11m Cement Grinder Mill is a specialized equipment designed for grinding clinker in cement production plants. Engineered for efficiency and high performance, this mill plays a crucial role ...
To investigate the effects of grinding media shapes on the grinding kinetics of ball mill cement clinker, the grinding effects with ϕ20 mm balls and ϕ20 × 20 mm cylinders on six different size ...
The questions of Portland cement clinker grinding in closed circuit ball mills. Noted that the main task of modeling the grinding process is predicting the granulometric composition of the finished product taking into account constructive and technological parameters used ball mill and separator. It is shown that the most complete and ...
حقوق النشر © 2024.Artom كل الحقوق محفوظة.خريطة الموقع