Mainstream production process of lithium iron phosphate
LiFePO4 prepared by the iron red process usually has poor performance, and the iron phosphate process is most likely to develop into a standard process for the preparation of lithium iron phosphate. Ferrous oxalate method. The ferrous oxalate method is a common preparation process in the early stage. Lithium carbonate and lithium hydroxide are ...
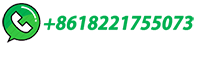