Advancing Cutting Tool Production with …
Julia Hider. Senior Editor, Modern Machine Shop. Electrical discharge grinding (EDG) enables manufacturers to produce cutting tools with stable cutting edges and complex features out of very hard …
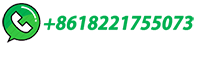
Julia Hider. Senior Editor, Modern Machine Shop. Electrical discharge grinding (EDG) enables manufacturers to produce cutting tools with stable cutting edges and complex features out of very hard …
Abstract. Electrical discharge grinding (EDG) is much like electrical discharge machining except that the electrode (tool) is a rotating graphite wheel. This article commences with a schematic illustration of a setup for EDG wheels and discusses the control operation of the EDG setup. It tabulates typical applications and conditions for the EDG ...
The machining system used in this experiment was a precision plane grinder MUGK7120×5 with a pulsed power source. The grinding wheel was connected with the anode of pulsed power source. ... Dry electro-contact discharge mutual-wear truing of micro diamond wheel V-tip for precision micro-grinding. Int. J. Mach. Tools Manuf., 60 …
Kent USA electrical discharge machines (EDMs) offer you the speed and accuracy to machine your parts successfully. Our Programmable Z-NC EDM's give you the control to burn with confidence and precision.
electrical discharge seems to be unavoidable and is the dominant factor for the flatness of machined surfaces [6]. Electrochemical discharge grinding (ECDG) combines the material removal actions of electrical discharge grinding with electrolytic attack to remove materials from electrical-ly conductive workpieces. There is a possibility that
Electrochemical discharge machining (ECDM) is a hybrid non-conventional machining process, used to machine electrically conductive and non-conductive materials. It is a preferred process to fabricate micro scale features like micro holes, micro channels, microgrooves and 3-dimensional intricate shapes on variety of materials. In order to …
What is Electrical Discharge Machining (EDM)? Electrical Discharge Machining, colloquially known as EDM, is a nonconventional machining process type …
For complex-shapes electro-discharge-machining (EDM) can be applied. Wire EDM (WEDM) is usefull for cutting shapes in materials with an minimum conductivity of about 0,01 s/cm. In our department ...
The paper reports the development of a new Abrasive Electrical Discharge Grinding (AEDG) system and investigations of performance characteristic of machining difficult-to-cut materials. Developed ...
n n All About EDM Machining (Electrical Discharge Machining) n. EDM Machining (Electrical Discharge Machining) makes it possible to work with metals for which traditional machining techniques do not work.Learn about Wire EDM,Sinker EDM,the history of EDM techniques,and more.Proses Electro Discharge Grinding …
Micro-machining and micro-grinding with tools fabricated by micro electro-discharge machining. Chris Morgan R. Vallance Eric R. Marsh. Engineering, Materials Science. 2006. This paper provides an overview of several approaches to micro-machining by mechanical and electro-discharge means of material removal. Two steps are required in machining ...
Micro-electrical discharge machining (micro-EDM) is a good candidate for processing micro-hole arrays, which are critical features of micro-electro-mechanical systems (MEMS), diesel injector nozzles, inkjet printheads and turbine blades, etc. In this study, the wire vibration of the wire electro-discharge grinding (WEDG) system has been analyzed …
Abstract. Electric discharge machining (EDM) is widely used to fabricate complex 3D geometries with a high aspect ratio in electri-cally conductive hard materials. EDM-milling (EDMM) is an advancement of EDM which can cut complex features at the micro-level with high accuracy and precision.
Koshy et al. explains the mechanism of the hybrid EDDG process, and how this mechanism improved the machining quality and rate through hybridization. Similarly, H. J. Zhang et al. [5], studied the same hybrid process under the name Electro Discharge Diamond wheel Grinding Machine (EDGM), to improve the machining of ceramic …
Electrical discharge machining, or EDM, is a non-contact process that can machine parts regardless of their hardness. It involves …
Since the development of wire-electro-discharge grinding (WEDG) technology, the micro-electrical discharge machining (micro-EDM) has been excellent in the process of fabricating micro-holes in WC-Co material. Even though high-quality micro-holes can be drilled by micro-EDM, it is still limited in large-scale production, due to the …
Electrical Discharge Machining (EDM) is a nonconventional machining process used primarily for tasks that would be unachievable with conventional methods. It uses electricity to erode the surface of conductive materials. Since no tool physically contacts the workpiece, EDM can maintain fine surface finishes even on intricate and …
In this research, the process of wire. electro discharge grinding (WEDG) b y using a li ne-segment wire discharge (called line-segment WEDG in this paper) were e xplored. for machining such ...
Electrical Discharge Machining (EDM) is a manufacturing process that shapes and forms metal parts using electrical discharges or sparks to remove material …
Abstract. Electrochemical discharge grinding (ECDG) is a combination of electrochemical grinding (ECG) and electrical discharge grinding (EDG), with some modification of each. This article commences with a schematic illustration of a setup for ECDG using a solid bonded graphite wheel. It describes the process characteristics of ECDG in terms of ...
Keywords: Grinding, Electro-chemical dressing, Electrical discharge machining 1 INTRODUCTION At present, economical and efficient grinding of modern cutting materials like cermets, PCD or ceramics can only be done by means of highly wear-resistant multilayer metal bonded grinding wheels, which, in turn, due to a lack of …
Electric discharge machining, also known as spark erosion, electro-erosion or spark machining, is a process of metal removal based on the principle of erosion of metals by an interrupted electric spark discharge between the electrode tool cathode and the working anode. Fundamentally, the electric erosion effect is understood by the …
Electrical Discharge Machining (EDM) is a manufacturing process that uses a combination of electrical and thermal energy to remove material from a …
Electrical discharge machining, or EDM, is a non-traditional method in which material is removed from a workpiece using thermal energy. Much like processes such as laser cutting, EDM does not need …
During past few years, a number of considerable researches have been made by the researchers over EDFG. Singh et al. [5, 6] proposed the optimization of parameters of electro-discharge diamond face grinding (EDDFG).Chow et al. [] have placed a rotating electrode below the workpiece and claimed that removal rate of debris is due to the …
Electrical discharge diamond grinding (EDDG), which integrates diamond grinding and electro-discharge machining (EDM), is a new hybrid machining process for shaping electrically conductive very hard materials. The process employs synergetic interactive effect of electro-discharge action and abrasion action to increase machining …
Electric discharge machining, also known as spark erosion, electro-erosion or spark machining, is a process of metal removal …
Electro Discharge Machining (EDM) is a thermal energy based non-traditional machining processes. Machining takes place due to continuous recurring of the electrons from cathode to the anode thus ...
Masuzawa T, Fujino M and Kobayashi K. Wire electro- discharge grinding for micro-machining. CIRP Annals, 34(1) (1985) 431-434. Masuzawa T, Yamaguchi M, Fujino M. Surface finishing of micropins produced by WEDG. CIRP Annals, 54(1) (2005) 171 – 174. Rajurkar KP, Levy G, Malshe A, Sundaram MM, McGeough J, Hu X, Resnick …
7.Texturing: EDT (Electro-discharge Texturing) is a process that involves using electrical sparks to create a surface texture on a workpiece, such as a roll. To do this, a tool electrode is positioned close to the workpiece and a high-intensity electrical spark is sent across the gap between the two. The gap is filled with a dielectric fluid ...
حقوق النشر © 2024.Artom كل الحقوق محفوظة.خريطة الموقع