Optimization of the Clinker Production Phase in a …
The most significant process of the cement production chain, in terms of energy efficiency and quality of the product, is represented by the production of the main …
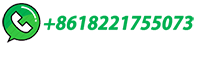
The most significant process of the cement production chain, in terms of energy efficiency and quality of the product, is represented by the production of the main …
Clinker is a granulated material made of raw meal powder obtained by grinding limestone and clay together by sintering the raw meal in a rotary furnace at 1400°C-1500°C …
3) grinding aid. Cost 0.6-1.2 €/t, usage 150-400 g/t. As the cement particle gets smaller the pores disappear and no longer become a factor. Increasing the amount …
the process of clinker grinding. Clinker hardness brings about a wide disp arity to grindability. About 80% extra power is . usually required in processing hard clinker tha n the soft ones ...
Cement Clinker Grinding Plant Play An Important Role In Process. Grinding plant of cement is an important topic when it comes to energy consumption. The clinker grinding ball mill is responsible for around 40% of the total energy usage during cement production line. Therefore intergrinding is a potential way of saving considerable amount of ...
First Online: 31 July 2020. 323 Accesses. 2 Citations. Part of the book series: Lecture Notes in Civil Engineering ( (LNCE,volume 95)) Abstract. Grinding processes in cement …
Clinker grinding process in cement plant. 3. Data collection and preprocessing. The quality parameter cement fineness is determined by offline laboratory analysis in terms of Blaine number which is defined as the surface area per unit mass (expressed in the units of m 2 /kg). High Blaine number indicates more fineness of the …
Finish Milling of Clinker. Finish milling is the grinding of clinker to produce a fine grey powder. Gypsum (CaSO 4) is blended with the ground clinker, along with other materials, to produce finished cement. The gypsum controls the rate of hydration of the cement in the cement-setting process.
Clinker Manufacturing Process. Cement grinding. Cement dispatch. All these steps are described in detail in the next sections. 2.1 Quarrying. The major raw material used in cement manufacture is lime. It is derived from materials such as limestone, chalk, marl, shale, and clay, which are obtained from mines by quarrying them.
Calcination is the main process of clinker production, calcining calcium carbonate (CaCO 3) at about 900 °C to form calcium oxide, CaO, lime, and the release of carbon dioxide gas (CO 2).In the next step of the so-called clinker treatment, calcium oxide (CaO) is exposed to temperatures of 1400 °C to 1500 °C together with silica (SiO 2), aluminum oxide (Al 2 …
On the contrary, the most common grinding process in cement plants is based on intergrinding of cement constituents in closed circuit units. The main difference between separate grinding and intergrinding is that during intergrinding the different minerals interact inside the mill. ... Assaad JJ, Issa CA (2014) Effect of clinker grinding aids ...
Clinker grindability is determined by quantity of electricity consumed for grinding (kW / ton) under other equal conditions. In cement production entire crushing and grinding process consumes about 85% of the electricity. At the same time 75% of electricity consumed for milling and only 2-20% of them consumed for grinding.
The grinding process involves reducing the clinker particles to a specific fineness, typically measured in terms of Blaine specific surface area or particle size distribution. The grinding process significantly influences the cement's strength development, setting time, and other performance characteristics.
Production Process of Clinker. Cement manufacturers create clinkers through a multi-step process that includes ingredient selection, heating, and grinding. Raw Mineral Preparation – The main ingredients …
Fig 4 shows material flows during the cement grinding. Clinker, gypsum, and additives are matched in required proportions by a weigh feeder, after which they are conveyed to the mill that performs the remaining grinding. The grinding process occurs in a closed system with an air separator that divides the cement particles according to size.
Electricity energy is required for different subprocesses such as clinker grinding, mining, and the clinkerization process. Therefore, electricity consumption could be estimated in two stages: from mining to clinkerization and for clinker grinding. ... heat consumption per unit in the production process of clinker is also reduced. This is a ...
A higher content of dihydrate in cement makes fine grinding easier, whilst hemihydrate has the opposite effect. The grain size distribution of cement is also affected by the amount and the mineralogical form of gypsum. ... The cement clinker manufacturing process traditionally involves intimate mixing and the subsequent heat treatment of a ...
Grinding of the clinker consumes about 1/3 of the power required to produce 1 ton of cem ent. This refers to an average specific power consumption o f 57 kW h/ton (W orrel et al ., 2002).
In this study we compare the effects of three different grinding aids on clinker grinding using a ball mill. A commercial grinding additive, triethanolamine (TEA), and two industrial grinding aids ...
Grinding processes in cement production technology are quite energy-intensive. The mechanism of action of surfactants on the course of the clinker grinding process has not been fully studied. According to the theory of P.A. Rebinder, surfactants change the mechanical properties of solids in the process of dispersion of materials.
Ordinary Portland Cement Clinker is the essential component in producing cement which is made by sintering limestone.In the manufacture of Cement, clinker formed by sintering or fusing without melting to the point of liquefaction, alumina-silicate materials such as clay and limestone during the cement kiln stage and happens as 3 millimeters (0.12 inches) to 25 …
"Chemistry" and "process engineering" constitute the foundation of the clinkerization process but over the decades the engineering advances have been …
The grinding process differs depending on the pyro-processing process used. The feed to the kiln is called "raw meal." Clinker is produced by pyro-processing the raw meal. The raw meal is burned at high temperatures, first by calcination of the materials and then by clinkerization to produce clinker. Various kiln types have been used ...
Explore the significance of clinker grinding in cement manufacturing, from particle size reduction to improved reactivity and quality control. Learn how this …
The use of a good Cement clinker grinding aid can be vital in today's increasing material demands. ... The potential significance of grinding aids in reducing energy consumption in the grinding process is illustrated by the examples in Tables 4-15 and 4-16. The unit operation of comminution, which is used extensively in a variety of ...
The main part of the manufacturing process of clinker takes place in the kiln. The stages in the kiln phase are as follows: Evaporation of free water: A pressure above atmospheric is …
The cement and clinker produced by indirect mechanosynthesis (15 min of mechanical activation and heat treatment 900 C or 1200 C) were characterized. In order to test the hydraulic properties of ...
Clinker grinding technology is the most energy-intensive process in cement manufacturing. Traditionally, it was treated as "low on technology" and "high on energy" as grinding circuits use more than 60 per cent of total energy consumed and account for most of the manufacturing cost. Since the increasing energy cost started burning the benefits …
Ball mills for fine grinding cement clinker and additives are widely used around the world. To improve the efficiency of a ball grinding the ball mills are transferred in closed circuit with air ...
Fuel costs are greater in the wet process than in the dry process because the water that is added to the raw materials to form slurry must be evaporated during the clinker manufacturing process. The clinker is then cooled down, mixed with gypsum and fed in specified proportions into a cement grinding mill where they are ground into an …
حقوق النشر © 2024.Artom كل الحقوق محفوظة.خريطة الموقع