Crushing Mechanics Of Crusher
mechanics of a stone crushing machine. Crusher - Wikipedia, the free encyclopedia A crusher is a machine designed to reduce large rocks into smaller rocks, gravel, ... The earliest crushers were ... Related Information. cost accounting for copper mining; mccrone micronizer mill for sale;
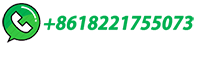