Coating and Burnability of Clinker | SpringerLink
In this method the sample of the kiln feed is taken and mixed with the coal ash in the same proportion as the coal is used per ton of clinker produced. The mixture of kiln feed and the ash is nodulized and burned at 1500 °C, and then the free lime is checked in it. The lower is the quantity of the free lime, the better is its burnability.
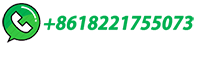