Crushing Iron
By Mike Tarrolly, Co-host of the Crushing Iron Podcast. An athlete I coach, Bill, left a training peaks comment the other day about how he went out for an easy run with a guy much younger and faster. Bill just finished …
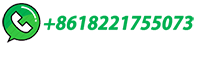
By Mike Tarrolly, Co-host of the Crushing Iron Podcast. An athlete I coach, Bill, left a training peaks comment the other day about how he went out for an easy run with a guy much younger and faster. Bill just finished …
Here, we find continuous suspension magnetization roasting followed by low-intensity magnetic separation can obtain a total iron grade of over 56% with an average value of 57.18% and a total iron ...
Hematite and magnetite, the two predominant iron ores, require different processing routes. High-grade hematite direct shipping ores generally only require …
Iron-containing ore beneficiation includes several stages. For example: crushing to 30 mm size class and rough magnetic separation, further crushing of the recovered magnetic product to 10 mm size class and final magnetic metal content upgrading. All operations use dry methods. Such an approach will concentrate relatively …
Iron ore tailings are industrial solid wastes generated from mineral processing. The disposal of iron ore tailings leads to environmental threat and serious security because of their tiny particle size and large storage. In this paper, suspension magnetization roasting and magnetic separation technology were utilized to recover …
The whole process philosophy is especially important when managing the crushing circuit, one of the biggest energy consumers in any plant. This is where optimisation of screening comes into play. ... Smith recalled a visit to an iron ore operation in Western Australia that was having trouble with a double-deck banana screen with a …
Iron ore crushing project The separation of coal and iron ore is typically done using magnetic separation or froth flotation. In magnetic separation, a magnetic field is applied to the mixture ...
Generally, magnetic biochar is manufactured by impregnating magnetic media such as iron, nickel, and cobalt species into a biochar matrix through either pyrolysis or post-treatment [5]. Magnetic ...
After high temperature holding and slow cooling treatment, the RO phase in the slag significantly grows, and therefore it is easier to be selected in the magnetic separation process after crushing. Multi-stage magnetic separation is the end of the first magnetic separation, that is, the magnetic substances undergo a new phase of …
Most of the high-grade hematite iron ores are typically subjected to simple dry processes of crushing and classification to meet the size specifications required for direct shipping ore (DSO). This involves multistages of crushing and screening to obtain lump (−31.5 + 6.3 mm) and fines (approximately −6.3 mm) products.
Magnetite Concentration Methods. Table of Contents. Magnetite is the most strongly magnetic of all minerals, and it is therefore natural that the earliest application of magnetism to ore dressing was for …
Iron ore beneficiation is mainly a process of separating valuable minerals and iron minerals from ores to extract high-quality iron ore. The iron ore process mainly includes crushing, grinding, washing, beneficiation, dewatering, etc. . Magnetite Beneficiation: The main iron mineral contained in magnetite is iron tetroxide (Fe3O4). And iron in the form of …
With an Fe grade of 65.25% at a recovery value of 72.5% in the concentrate, magnetic separation produced the greatest result for Fe. The performance of magnetization and …
Iron ore has a special place in the global mining industry, judging by the volumes of ore processed and the energy usage. ... AG milling in closed circuit with hydrocyclones and pebble crushing – rougher magnetic separation – ball milling – cleaner magnetic separation – tertiary milling using stirred mills – second cleaner magnetic ...
The main iron ore mining equipment includes jaw crushers, ball mills, magnetic separators, spiral classifiers, jig concentrators and related auxiliary equipment such as ore dryers. Jaw crusher reduces the hard iron ore into a smaller size, it has a high iron crushing ratio, feeding and crushing capacity, uniform texture, good grain shape.
Primary crushing followed by wet SAG or AG milling and ball or pebble milling. Air-swept AG milling (for coarse grind). Historically, the lowest operating cost for fine-grained ores was achieved by multi …
Iron-containing ore beneficiation includes several stages. For example: crushing to 30 mm size class and rough magnetic separation, further crushing of the …
sbm cone crusher in magnetic iron ore crushingcone crusher made in pakistan iron ore plant design Cone Crusher Used in Pakistan Iron Ore Mining Cone Crusher Used in ...
The banded iron formation of Banded Hematite Jasper is a very low grade iron ore that usually contains Fe in the range of 30-40% depending on the origin. Banded hematite Jasper obtained from Barbil region of India and assaying 41.9% Fe, 38.4% SiO 2 and 0.4% Al 2 O 3 was studied for pre-concentration of iron values adopting Jigging and …
Iron ore tailings (IOTs) are a form of solid waste produced during the beneficiation process of iron ore concentrate. In this paper, iron recovery from IOTs was studied at different points during a process involving pre-concentration followed by direct reduction and magnetic separation. Then, slag-tailing concrete composite admixtures …
The major benefit of fully autogenous grinding is the elimination of steel grinding media costs and the need to discriminate between steel and magnetite in coarse magnetic …
Whatsapp (price): +86. An impact crusher with a magnetic separator refers to a type of crushing machine that utilizes the principle of impact crushing to reduce the size of materials ...
Fig. 1 Schematic diagram of the crushing (a) Impact crushing; (b) Shear crushing 2 Results and discussion 2.1 Preparation of high-performance anisotropic NdFeB Magnets The bulk anisotropic magnets were prepared by hot- deformation with different height reduction and the ap- pearance of the crack-free HD magnet is shown in Fig. 2(a).
Volume 23, March–April 2023, Pages 2362-2370. Original Article. Efficient separation of iron elements from steel slag based on magnetic separation process. Xin …
"The remarkable process of crushing and magnetic separation of iron ore at Mr. Thomas Edison's works in New Jersey shows a characteristic originality and freedom from the trammels of tradition ...
As a result of dry magnetic separation at about 750 Gauss magnetic field conducted with -0.212+0.106 mm size fraction under optimum conditions, a magnetite concentrate assaying 54.41% Fe was ...
In the recent past, iron ore resources from Brazil consisted of relatively high-grade iron ore, commonly processed via multi-stage crushing/screening, gravimetric concentration, magnetic separation, and reverse flotation. However, the high-grade iron ore reserves are in decline, resulting in the need to process the lower grade itabirite iron …
After passing through several rollers and mesh screens, the finely crushed material falls in a thin sheet in front of a series of magnets, which deflect the magnetic …
Iron is the most magnetic of the three. The principle ores of iron are hematite, (70% iron) and magnetite, (72% iron). Taconite is a low-grade iron ore, containing up to 30% magnetite and hematite. Iron Mining. ... Large raw iron ore for primary crushing are fed into the jaw crusher by Plate feeder and are reduced to 8 inches or smaller. After ...
1. Introduction. Iron-containing ore beneficiation includes several stages. For example: crushing to −30 mm size class and rough magnetic separation, further crushing of the recovered magnetic product to −10 mm size class and final magnetic metal content upgrading. All operations use dry methods.
حقوق النشر © 2024.Artom كل الحقوق محفوظة.خريطة الموقع