Major Mines & Projects | Sishen Mine
Iron Ore; Mining Method: Truck & Shovel / Loader; Processing: Jig plant; Crush & Screen plant; Wash plant; Dense media separation; Production Start: 1953: Mine Life: 2038
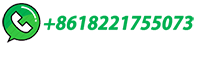
Iron Ore; Mining Method: Truck & Shovel / Loader; Processing: Jig plant; Crush & Screen plant; Wash plant; Dense media separation; Production Start: 1953: Mine Life: 2038
Application: gold, diamond, coltan, tin, tungsten, titanium, manganese, tungsten ore, fluorspar ore, iron ore, chrome ore, etc mineral processing plant. ... rotary scrubber, gold sluice box and other equipment to form a small-scale mobile jig plant, used in gold and diamond washing processing plants. High recovery rate – recover 0.5% to 30% ...
. A jigging machine is a piece of equipment that implements the jigging process. The process in which the material is sorted according to density differences, mainly in a vertically rising and falling stream of variable speed media. The difference in size and shape of the material has an effect on the result of the separation.
Beneficiation of fine iron ore fines was studied in Kelsey Jig. A constant pulp density (25% solids) of the feed slurry was maintained in the study. The feed rate was also kept constant at 60 kg ...
Until the early twenty-first century, iron ore mines developed in Brazil focused primarily on hematite bodies. These ore bodies typically had over 60% Fe and low levels of contaminants (such as Al 2 O 3 and SiO 2), and produced lumps (>16 mm) with physical, chemical, and metallurgical properties favorable for extraction. In the Quadrilatero …
Optimum iron ore recovery of 78.6% was achieved with 63.7% Fe in concentrate when the jig was operated at medium stroke, with an average water velocity and at a particle size of below 5 mm.
Kumba Iron Ore, part of AngloAmerican, operates the Sishen and Kolomela mines in the Northern Cape region of South Africa. The mines utilise a number of processes for handling and upgrading the ore, including direct shipping, screening, upgrade jigs (including one of the largest jig plants in the world), and dense medium separation. The processes allow …
Barsua iron ore mines, a captive iron ore mines of Rourkela Steel Plant, has adopted Remco Jigs for the beneficiation of low-grade iron ore fines at a size range of − 8 + 2 mm. Similarly, a Batac jig has been installed to reduce alumina content from the Noamundi iron ore fines of Tata Steel and the Apic jig used in iron ore mines of South ...
Kumba Iron Ore's Sishen mine in South Africa produces 41 Mt of iron ore per annum from its beneficiation plants. The orebody consists mainly of laminated and massive haematite ore, of which 34 M/a is crushed to -90 mm before beneficiation by means of a …
Beneficiation Of Hematite Iron OreFirst Latest Special Jigging Plant For Hamatite Iron Ore In India Emf Tech Jig Is A Simple Mineral Processing Device Using Water And The Force Of Gravity To Separate A Raw Ore Stream By Density. In Many Applications This Permits A Low Grade Ore Stream To Be Upgraded In Quality Sufficient For Sale: Gangue Of …
Plant. Full resource and mineral production - DMS - Scrubber - Wet plant - Crusher - Jig - Active testing between weighbridge Production. In a world of declining quality iron ore supplies, our iron ore operations are positioned to supply premium products to our customers, helping meet ever growing demand. ... These iron ore reserves are all of ...
MYBURGH, H.A and NORTJE, A. Operation and performance of the Sishen jig plant. J. S. Afr. Inst. Min. Metall. [online]. 2014, vol.114, n.7, pp.569-574. ISSN 2411-9717. Sishen Iron Ore Mine previously used only A-grade material (>60% Fe in situ value) from the pit for beneficiating in the DMS plant to a final product grade of 66% Fe in lump and ...
A DELKOR APIC jig was supplied as part of a contract to provide plant engineering for the complete crushing, screening and jigging plant for iron ore beneficiation. The jig, was at the time of the contract, the largest in the iron ore beneficiation industry in India, and is an important reference for 4 m wide APIC jigs.
OK. The server encountered an internal error or misconfiguration and was unable to complete your request. Apache/2.2.6 (Fedora) Server at eprints.nmlindia Port 80
Operation and performance of the Sishen jig plant. J. S. Afr. Inst. Min. Metall. [online]. 2014, vol.114, n.7, pp.569-574. ISSN 2411-9717. Sishen Iron Ore Mine previously used …
Jig Concentrator Types. The trapezoidal jig separator machine has a large processing capacity and a wide particle size of 50-0.25 mm. It has been promoted and used in tungsten, tin, and iron ore dressing plants. According to the beneficiation medium, mineral jig divided into the hydraulic jig and dry jig, dry material feeding has a better result.
A commercial jig plant has been installed in South Africa to recover metal concentrate of 97% grade at 76% metal recovery from minus 1mm ferrochrome slag far exceeding conventional gravity methods ...
Abstract. Sishen Iron Ore Mine previously used only A-grade material (>60% Fe in situ value) from the pit for beneficiating in the DMS plant to a final product grade of …
1. Crushing & Screening: jaw crusher, cone crusher, vibrating screen. Vibrating feeder evenly feeds the jaw crusher. jaw crusher crush big rock, Then transport it to the vibrating screen with a belt conveyor, and screen out two kinds of materials, +20MM, 0-20mm. The +20MM material is conveyed to the cone crusher by a belt conveyor with an iron ...
Development of a beneficiation route to upgrade Sishen iron ore jig slimes for iron making Molebiemang G.M 208023232 ... while the remaining 10 Mt is processed by the jig plant that was added as an expansion to the DMS processing route. The jigs at the jig plant are employed to treat coarse, medium and fine Run of Mine ...
JXSC jig concentration machine is energy-saving gravity separation equipment, which is developed according to the law of layer theory of jigger bed stratification. The performance
Spiral concentrators are used in the iron ore industry to separate heavy iron oxide carrier particles from the light silica ones. Losses of iron occur mainly in the fine (− 75 μm) and coarse (+ 600 μm) size fractions.This paper analyzes the radial distribution of iron oxide and silica particles in the reject of a 7 turn spiral.
Jul 11, 2018· The JIG plant was constructed in 2007, with the aim of improving the quality of the product to 63% iron (Fe), while the new ultra-high-density plant will recover ore from the JIG discards. Sishen's DMS plant has a capacity to process 22Mt of product in the range of 64–65% Fe. Read More.
Sishen Iron Ore Mine previously used only A-grade material (>60% Fe in situ value) from the pit for beneficiating in the DMS plant to a final product grade of 66% Fe in lump and 65% Fe fine ore. The B-grade (between 50% and 60% Fe) and C-grade material (between 35% and 50% Fe) were stockpiled separately, owing to the inability of the …
Optimum iron ore recovery of 78.6% was achieved with 63.7% Fe in concentrate when the jig was operated at medium stroke, with an average water velocity and at a particle size of below 5 mm. The results are very close to theoretical results obtained by sink and float studies. Keywords: Low grade iron ore, mineralogy, jigging, particle size ...
In the present study a detailed characterization followed by beneficiation of low grade iron ore was studied. The Run of Mine (R.O.M) sample assayed 21.91 % Fe, which is very low grade in nature.
The feed material to the jig plant at Sishen Iron Ore Mine is reduced to a -25 mm top size in a three-stage crushing circuit and longitudinally stacked on two pre-beneficiation feed beds
The Concentrate contains a Fe grade of > 66%. A further capacity expansion project to 16 Mtpa product is currently underway using 3 more BATAC jigs. The first large scale Iron Ore Jig beneficiation plant in India was commissioned in 2006 at Noamundi in the state of Jharkhand. Tata Steel is already operating a 300 tph Fine Ore BATAC Jig Iron Ore ...
Sishen Iron Ore Mine previously used only A-grade material (>60% Fe in situ value) from the pit for beneficiating in the DMS plant to a final product grade of 66% Fe in lump and 65% Fe fine ore. The B-grade (between 50% and 60% Fe) and C-grade material (between 35% and 50% Fe) were stockpiled separately, owing to the inability of the …
2. The jaw crusher crushes 50-230mm iron ore into the fine jaw crusher. Spiral washing machine is suitable for cleaning 0-50mm materials. 3. The fine jaw crusher crushes the material to 0-20mm. The vibrating screen sends the 0-20mm material into the ball mill, and the +20mm material returns to the fine jaw crusher.
حقوق النشر © 2024.Artom كل الحقوق محفوظة.خريطة الموقع