(PDF) The Effects of Blasting on Crushing and Grinding
The final product is 80% passing 270 mesh. ... Crushing and grinding calculations Part II. Article. Jan 1961; F.C. Bond ... The effects of blasting on crushing, grinding efficiency and energy ...
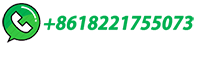