Strengthening pelletization of manganese ore fines …
Pelletization is one of useful processes for the agglomeration of iron ore or concentrates. However, manganese ore fines are mainly agglomerated by sintering due …
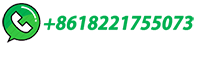
Pelletization is one of useful processes for the agglomeration of iron ore or concentrates. However, manganese ore fines are mainly agglomerated by sintering due …
Highlights The pelletizing pressure is an important parameter in biomass pelletization processes. The pressure has to be kept in a range where high quality pellets are produced, at a minimal energy input. Major parameters affecting this pressure were pellet length, temperature, moisture content and particle size distribution. Pelletizing …
For pelletization, torrefied/carbonized agricultural residues are usually mechanically pressed using screw or piston press and at times using high temperature and pressure . Addition of binders can agglomerate the carbonized biomass particles, in order to enhance the pellet density, durability, transportability and compressive strength [ 31 ].
In this work, ceramic superconductors with nominal composition Bi1.8Sr2Ca1.1Cu2.1Oy were produced by different pelletization pressures at high values varied from 1.5 GPa to 6 GPa. The effects of high pelletization pressure on the structural and magnetic properties of samples fabricated in this work were investigated by means …
The lower temperature and pressure reached during pelletization in combination with a high content of extractives and low proportion of lignin could explain this behavior. Waxes and fats present in the extractives have a double effect, diminishing the friction in the die channels and preventing the formation of strong bonds through the ...
Varying pelletization pressure for untreated pellets made at 200 °C affected mass density with values ranging from 797.3 to 1333.1 kg m −3 and as a result, ... and high pelletization pressure favor the pelletization. However, a techno-economic analysis might be warranted to optimize the torrefaction and pelletization conditions. …
We reported the evaluation of superconducting properties of Bi-2212 ceramics prepared under different dwell times between 12 and 72 h under 114 MPa constant pelleting pressure using precursors produced through the conventional solid-state reaction. From the XRD patterns, it is clear that all samples contain a high Bi-2212 …
In addition, the pelletization pressure and temperature significantly impact the pellets' durability, bulk, and energy density. Process parameters, including pelletization pressure and temperature of Khaya senegalensis biomass, will be determined to produce high-quality pellets. Proper implementation of pelletization parameters is essential ...
The hole concentration H increases with the increase of the pelletization pressure up to 1.4 GPa. This is an important suggestion for the improvement in the …
Pelletization is a form of the process through agglomeration that transforms granules of bulk drug powders into pellets (Kandukuri et al., 2009). It is frequently denoted as a size-amplification ...
The pelletization process is the primary consumer of binders in the iron ore industry. The selection of an appropriate binder type and dosage is of critical importance in producing good quality pellets at a reasonable price. Binders accomplish two very important functions in iron ore pelletization: .
Abstract. A study of pelletization of one imported chromite concentrate with coarse size, poor ballability and refractory roasting performance was conducted in small scale tests, and high pressure ...
Pelletization is one of useful processes for the agglomeration of iron ore or concentrates. However, manganese ore fines are mainly agglomerated by sintering due to its high combined water which adversely affects the roasting performance of pellets. In this work, high pressure roll grinding (HPRG) process and optimization of temperature …
The optimization results showed that high quality pellets could be produced at a pressure of 68.4 MPa, temperature of 110.0 °C, and moisture of 8.2% for solid …
However, higher pressure consumes high energy, and energy consumption must be kept to a minimum while achieving the techno-economic feasibility of the pelletization process. Herbaceous biomass requires less energy to pelletize as they are easy to compress compared to woody biomass (Cui et al. 2021 ).
The variation of (T c) as function of the pelletization pressure is shown in figure 4. (T c) is observed to increase with increase the pelletization pressure from 0.3 GPa up to 1.4 GPa, T c = 110 K. It is well known that the values of (T c) are based on the properties of inter-grain related to the weak or strong coupling between the grains
Pelletization process parameters are also considered together with the basics of pelletization modeling both for flat die machines and ring die machines. A model is applied to the pelletization of biochar, that allows the comparison with spruce fir wood. ... Due to high pressure and high temperature conditions, the diffusion of molecules from ...
A study of pelletization of one imported chromite concentrate with coarse size, poor ballability and refractory roasting performance was conducted in small scale tests, and high pressure grinding ...
The effect of pressure of pelletization and sintering temperature with different synthesis routes on dielectric, impedance and ferroelectric properties has been studied earlier [13, 14]. Lanthanum ...
The applied pressure during the pelletization process activates the different binding mechanisms as the natural binders as starch, protein and lignin in the material are pressed out and produced good inter-particle bonding [10], [46]. Durable and hard …
A lab-scale single-channel press was employed for producing pellets and the effect of pressure, die temperature, moisture content (MC), particle size, and binding agent on pellet quality was investigated. Meanwhile, torrefaction subsequent to pelletization was performed and the quality of pellets was evaluated under different torrefaction …
The effects of high pelletization pressure on the structural and magnetic properties of samples fabricated in this work were investigated by means of X-ray powder diffraction, scanning electron ...
The effects of high pressure up to 600 MPa on various properties of Bi 2 Sr 2 CaCu 2 O 8+ ... Abdulridha, A.R., Bermany, E.A., Hashima, F.S., Alkhayatt, A.H.O.: Synthesis and characterization and pelletization pressure effect on the properties of Bi 1.7 Pb 0.3 Sr 2 W 0.2 Ca 2 Cu 3 O 10+ ...
The mechanical pressure applied to the particles during pelletization reduced the dimensions of the constituent particles. The highest percentage of particles in soft wood pellets (∼30%) in the size range of 0.5–1.0 mm can be attributed to the size reduction action during pelletization.
Abstract. High-density ThO/sub 2/-2% UO/sub 2/ (/sup 233/U) pellets are a strong candidate fuel for advanced pressurized heavy water reactors. A process flow sheet based on sol-gel microsphere pelletization has been developed for the first time for fabrication of high-density mixed-oxide pellets at relatively low compaction pressures (350 MPa) and …
Pelletization is a suitable method to improve the characteristics of biomass feedstocks for both heat and power generation [ 7 ]. Wood pellets are cylindrical pieces, …
The pelletization of rich manganese ore powders containing high combined water was investigated via raw-material pretreatment by high-pressure roll grinding to obtain pellets with high mechanical ...
In contrast to varying temperatures, pelletizing at different pressures led to lower axial and diametral compressive strengths. This suggests that a high pelletization temperature can improve …
The pelletization process is very widely used, particularly when burden materials must be shipped great distances between the mine and the blast furnace, because fired pellets are durable and easy to handle. ... Discussion here will be focused on pretreatment methods, including damp milling, ball milling, and high-pressure grinding …
Wood welding, like pelletization and briquetting, is a process where heat and pressure is applied to biomass, resulting in bond formation. The mechanism behind friction welding of wood has been studied in great detail (Delmotte et al. 2008, 2009; Mansouri et al. 2010; Pizzi et al. 2006).
حقوق النشر © 2024.Artom كل الحقوق محفوظة.خريطة الموقع