A novel direct reduction-flash smelting separation process …
A new process (direct reduction and flash smelting separation (FSS)) of treating high phosphorus iron ore (HPIO) is introduced in this paper. By limiting the smelting separation between slag and iron to the level of about 1 s, the reduction and migration process of P element was restrained, and the content of P element in the …
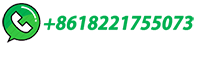