iron ore crusher plant design step by step
Home News iron ore crusher plant design step by step. 16 Dec 2023. Step 1: Define the project requirements. The first step in designing an iron ore crusher plant is to define the project requirements. This includes the following: The type of iron ore that will be processed. The desired output of the plant.
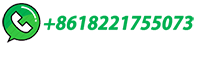