Know All About Cement Manufacturing Process in India | mycem cement
Mining of limestone. Raw material preparation / raw mix preparation. Crushing. Homogenization. Proportioning of raw materials. Grinding. Storing and Blending. Burning of raw mix. Clinker grinding along with gypsum – Cement.
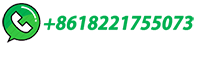