CEMENT | Capitol Aggregates
Capitol Type N Masonry cement is recommended for use in exterior walls, retaining walls, manholes, sewers, pavements, walls and patios above grade. It can be used in load-bearing walls, both interior and exterior. Capitol Type N Masonry cement is available in 70.5 lb (32Kg) bags. PRODUCT DATA SHEET. MILL CERTIFICATE.
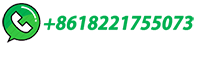