Study Of The Effect Of Binder Types On The Reduction …
Processing it into Direct Reduced Iron (DRI) or sponge iron is considered to be the right step to increase its value. In the DRI making, firts, iron sand will be agglomerated using binder and compaction to form briquette shape. ... keywords = "binders types, direct reduction, titanomagnetite iron sand, tunnel kiln", author = "Sungging ...
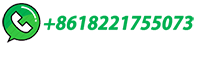