Iron Ore Processing Plant in Ethiopia
Iron ore extraction equipment refers to iron ore mining equipment used in the beneficiation process of iron. Zenith's dry magnetic separator is widely used in the …
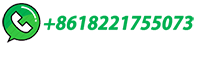
Iron ore extraction equipment refers to iron ore mining equipment used in the beneficiation process of iron. Zenith's dry magnetic separator is widely used in the …
Cleveland-Cliffs recently completed a $100 million expansion at its Northshore Mining operation to support large-scale commercial production of DR-grade pellets. With its completion, Northshore Mining is now the only U.S.-based iron ore processing facility to produce low silica DR-grade pellets. The Northshore operation is producing DR-grade ...
It is concluded that high grade iron ore concentrate can be produced for direct reduction in iron and steelmaking, with high recovery and a smaller footprint. …
The Pineer froth flotation process enables sustainable and cost-effective spodumene/lithium ore recovery. Comes from one supplier, responsible for the whole package. Provides mechanical and performance guarantees for the entire plant machinery, with clear battery limits for engineering and implementation. Provides optimal process …
An Study on Preparation and Utilization of Tourmaline from Tailings of an Iron-ore Processing Plant ... China's Non-metallic Mining Industry Guide. 2004(5)Ë–56-58. 3. Chen X, Hu Y, Li Y et al. Modification of tourmaline powder and lately development as well as research progress, Inorganic Salt Industry, 2013(5); 5-8. 4. Huang Y, Zheng S, Li ...
Current industrial practice of processing of iron ore fines in India does not involve much beneficiation. However, few plants in India are treating fines during washing, classification, and jigging process [4]. In other parts of the world, iron ore fines are beneficiated for magnetite- and hematite-rich iron ore in * P. Dixit prashant.dixit ...
Sesa Goa Iron Ore, a Vedanta Group company, is engaged in the exploration, mining, and processing of iron ore. The company was founded in 1954, as Scambi Economic SA Goa. Since then, it has grown to be one of the country's top low-cost producers of iron ore. During 1991-1995, it diversified into pig iron and metallurgical coke manufacturing.
Iron ore handling, which may account for 20–50% of the total delivered cost of raw materials, covers the processes of transportation, storage, feeding, and washing of the ore en route to or during its various stages of treatment in the mill.. Since the physical state of iron ores in situ may range from friable, or even sandy materials, to monolithic …
Making iron and steel from iron ore requires a long process of mining, crushing, separating, concentrating, mixing, agglomeration (sintering and pelletizing), …
The Ally to Your Iron Ore Processing Plant. Here at Benetech, we dedicate our greatest resources to resolving your daily challenges in bulk material handling. To discuss how you can reinforce a safer, more productive iron ore facility, contact us at (630) 844-1300 to speak with a specialist. Posted in Dust Control.
As evident in Fig. 1.2, the world's production of usable (processed) iron ore has increased from about 970 million tons in 2000 to 2.45 billion tons in 2019. Australia is the largest iron ore producing country, producing approximately 919 million tons of usable ore in 2019, equivalent to about 37% of the world's iron ore production.
Dry iron ore processing The mining activity produces lots of materials with no commercial value. That is because the iron ore traded in the market must be composed of at least 58% of ore.
Dry processing of iron ore: In dry processing of iron ore, ROM is generally crushed below 40 mm through three-stage crushing and thus segregated by screening into 10–40 and −10 mm fractions. For softer ore, tumbler index is generally low and hence lump ore is crushed below 10 mm to produce fine product. Yield from the plants has …
Abstract. Mining of iron ore is a highly capital- and energy-intensive process. Life cycle assessment (LCA) of the mining and mineral processing of iron ore in Australia was carried out in this chapter using SimaPro LCA software as a case study. The environmental impacts considered in the study were embodied energy and greenhouse …
The Kolomela Mine is situated near Postmasburg Town in the Northern Cape Territory in South Africa. Mining operation at Kolomela started in late 2011. A stacker-reclaimer is used at Kolomela to blend different grades of processed ore before shipment. Kolomela produced 13.2Mt of direct shipping iron ore in 2019.
Iron ore processing by Rio Tinto in the Pilbara region of Western Australia does not involve any chemical treatment. Flowsheets for the Brockman 2 and Paraburdoo processing plants are given in Figures 8.4 and 8.5 (Kinnel, 2013). The flowsheets are relatively simple. Dry processing involves up to three crushing circuits to produce lump …
iron ore refining process plant – Mineral Processing Plant … processing, smelting, refining, and marketing of iron, manganese and chrome ore. Home; … for easy export of the metal ore products.
Typical Iron Ore Beneficiation Flow Sheet. Multotec specialises in iron ore beneficiation equipment with over 50 years of global experience and leading technology. Our team of metallurgists and engineers will partner with you …
Activities involved in finding, mining and processing iron ore at our Pilbara operations have been simplified in the following diagram. Rio Tinto operates 11 iron ore mines in the Pilbara and the specific sequence of activities varies from mine to mine. Excellence in planning, scheduling and quality control are fundamental to the process.
At the processing plant, the taconite is crushed into very small pieces by rock crushing machines. The crushers keep crushing the rock until it is the size of a marble. The rock is mixed with water and ground in rotating mills until it is as fine as powder. Separation The iron ore is separated from the taconite using magnetism.
The three primary and secondary crushing stations each crush 5000 tons of ore an hour (t/h) into particles smaller than 150 mm. This material is then conveyed to a 250,000 t surge stockpile prior to being fed into the processing plant. When the ore is fed into the processing plant it first enters the scrubbers, before being sent to wet screening.
This Plant used for gold, copper, iron ore etc. Process of Ore Processing Plant: the ore is first sent to the jaw crusher for primary crushing. Then the ore with a proper size for secondary crushing will be sent into the ball mill for fine crushing and grinding. The ore powder discharged from the ball mill will be sent to the next procedure ...
IRON ORE PROCESSING AND STEEL MAKING Iron Expected Resource 250 Million tons Iron content 30% Available at mine mouth Coal Coke substituted by Coal in Corex Technology Locally Available Raw Material Dolomite & Limestone available in Salt Range, Punjab Others Availability of surplus Power (Demand 300 MW) Water Availability …
The authors present engineering solutions aimed at designing energy-efficient horizontal-grate calcinator MOK-1-592 and the technologies to produce …
1. Crushing & Screening: jaw crusher, cone crusher, vibrating screen. Vibrating feeder evenly feeds the jaw crusher. jaw crusher crush big rock, Then transport it to the vibrating screen with a belt conveyor, and screen out two kinds of materials, +20MM, 0-20mm. The +20MM material is conveyed to the cone crusher by a belt conveyor with an iron ...
Primero Group says it has completed the construction of a Wet High Intensity Magnetic Separation (WHIMS) processing plant at Fortescue Metals Group's Christmas Creek iron ore mine in Western Australia. The plant is expected to improve product grade and mass recovery from the desands unit at the Christmas Creek Ore Process Facility …
Making iron and steel from iron ore requires a long process of mining, crushing, separating, concentrating, mixing, agglomeration (sintering and pelletizing), and shipping …
The Philippines is looking to follow in the footsteps of its neighbour Indonesia, which has successfully attracted massive investment into processing plants for its huge nickel ore deposits, after ...
Iron processing, use of a smelting process to turn the ore into a form from which products can be fashioned. Included in this article also is a discussion of the mining of iron and of its preparation for smelting. Iron (Fe) is a relatively dense metal with a silvery white appearance and distinctive.
Sierra Metals Inc. has announced that its Board of Directors has approved the investment by the company of US$28 million for the construction of a magnetite processing plant, including an initial expenditure of US$5.2 million for early procurement and contracting on the project. The plant is expected to produce approximately 500 000 …
حقوق النشر © 2024.Artom كل الحقوق محفوظة.خريطة الموقع