Copper Mining and Processing: Everything you Need …
The Copper Mining Process. Once it's located within the earth, copper ore goes through eight stages before the consumer sees it …
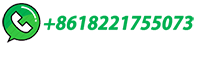
The Copper Mining Process. Once it's located within the earth, copper ore goes through eight stages before the consumer sees it …
Copper Fact 5. Pure copper's melting point is 1,981°F (1,083°C, 1356°K). ... 2007 U.S. Mine Production Compared with Current USGS Estimates of Copper Reserves and Resources; ... CuproBraze™ is the name of a new manufacturing process for copper-and-brass automotive radiators. The process uses fluxless lead-free brazing, anneal …
One former Roman copper mine and smelting site in Wadi Faynan, Jordan is still — two thousand years after it ceased operations — a toxic wasteland littered with slag from copper smelting. Researchers have discovered that vegetation and livestock in Wadi Faynan today have high copper levels in their tissue.
By contrast, a mismatch of 10 °C in allowable temperature or 0.21 W cm−2 in heat flux can be eradicated by a full filling of copper in paraffin. Specifically, the copper extends the effective protection time by enhancing heat conduction at β ≤ 60%, then it is further prolonged by improving the natural convection at β>60%.
1. Introduction. Copper is an important metal for the global development. Owing its chemical, thermal, electrical, and mechanical properties, copper is widely used for electrical and electronic equipment, construction, infrastructure, industrial processes, and transport [1].To fulfill the world́s copper demand, copper production by mining has been …
The Basics of Copper Mining and Processing. Mined from open pits, copper ore must be crushed as part of the process that occurs between extraction and production. Using today's compact mining …
The Contimelt process is suited to handle both blister copper and scrap copper to produce copper anodes for the tankhouse. The following description provides …
World copper mine output in 2002 was 13.3-million metric tonnes and is anticipated to reach 14 million by the beginning of 2004. ... and Mitsubishi ranges from 23 to 25 GJ/tonne of copper for the process consisting of concentrate drying, smelting and converting, fire refining ... Units may be used to melt copper cathodes and selected high ...
Copper is a chemical element in the periodic table with the symbol Cu (from the Latin word cuprum, meaning 'metal of Cyprus,' where it was mined during the Roman era). Copper has an atomic number of 29 and atomic weight of 63.54 grams per mole. It is an element in Group 11 of the periodic table, sharing many properties with silver and gold.
Copper smelting is an ancient process that defies modern technology. In essence, it involves extracting copper from its ore and melting it down to create pure copper. The copper smelting industry is a critical component of the modern economy, producing much of the copper necessary for manufacturing and construction …
2. In copper processing, a copper cathode is the final, 99.99% pure product of the electrolysis process, and is itself the primary raw material input for the production of finished copper products, such as rode, tubes, and wires. cation: A positively-charged ion that is attracted to the cathode (negative terminal) in electrolysis.
2. Message from the ICAA The Zero Emission Mine of the Future was commissioned by the International Copper Association Australia Ltd (ICAA), the pre-eminent marketing arm of the Australasian copper industry that is closely aligned with the International Copper Alliance.
Copper Flotation. As a commonly used process for copper ore beneficiation, flotation can be used for the separation of copper sulfide and oxidized copper ores. The main process of copper ore flotation is rough as follows: ore crushing and screening → stage grinding stage flotation → concentration and dehydration → copper concentrate.
Roasting, smelting., and converting. Once a concentrate has been produced containing copper and other metals of value (such as gold and silver), the next step is to remove impurity elements. In older processes …
An induction furnace for copper melting consists of essential components that work together to facilitate the melting process. These components include: Induction Coil and Power Supply: The induction coil, utilized in the induction copper melting furnace, generates a powerful magnetic field inducing electrical currents in the copper.
3. 3. Processing of Copper Ore. Top: Sulfide ore processing. Bottom: Oxide ore processing. The process varies slightly depending on the type of ore that is being mined. Sulfide ores are first put through a jaw or gyratory …
1. Introduction. The copper smelting industry is an important part of the traditional non-ferrous industry, as well as a basic component of the emerging communication and new energy industry (Dong et al., 2020).In the past 10 years, global primary copper smelter production has increased by more than 40% and showed an …
cobalt processing, preparation of the metal for use in various products. Below 417 °C (783 °F), cobalt (Co) has a stable hexagonal close-packed crystal structure. At higher temperatures up to the melting point of 1,495 °C (2,723 °F), the stable form is face-centred cubic. The metal has 12 radioactive isotopes, none of which occurs naturally.
Experimental procedure 2.1. Melting process First, 3 slag samples are obtained by melting mineral concentrates, using PbO 2 as a flux in the melting process. Melting is carried out in a Lindberg furnace at 1000°C during 1 h. The PbO 2 is reduced to a metallic Pb, which collects the precious metal.
The first step, mineral processing, is to liberate the copper minerals and remove waste constituents—such as alumina, limestone, pyrite, and silica—so that the copper minerals and other nonferrous minerals of …
Copper Production Copper production is not an environmentally benign activity. From mining and milling through hydro- and pyrometallurgical processing to refin-ing, copper production can have significant ad-verse impacts on air quality, surface and ground-water quality, and the land (see figure 8-1 ). While these impacts can be severe when the ...
3.1 Reduction Characteristics of Slag. In the blister-making period of converter smelting, blister copper coexists with fayalite-based slag, and a large amount of magnetite precipitated in the melt when the Cu–Fe–S–O–SiO 2 system was equilibrated at high oxygen potential. Analysis of the copper converter slag used in this study indicates …
After mining, copper is produced by one of two process routes: pyrometallurgical or hydrometallurgical. Within the pyrometallurgical route, the mined ore is crushed and milled, followed by a concentration step using flotation. The obtained copper concentrates contain on average 30 percent copper, but grades can range from 20 - 40 percent (ICSG ...
Production: 1.13 million MT. BHP produced 1.13 million MT of copper in 2022 and operates two mines in Chile and one in Peru. The first is Escondida, the world's largest copper mine, which is an ...
Copper Production. Hong Yong Sohn, ... Bart Blanpain, in Treatise on Process Metallurgy: Industrial Processes, 2014. 2.1.1.6.1 FeO–Fe 2 O 3 –SiO 2 Slags. It has been customary since early times in copper smelting, when acid refractories were used universally, to add SiO 2 to form a slag with the iron that has been oxidized. This is still the most common …
copper processing, the extraction of copper from its ores and the preparation of copper metal or chemical compounds for use in various products. samovar. Copper samovar. In its pure form or as an alloy, …
Innovating the smelting process. Induction furnace for melting ferrous and nonferrous metals, including precious metals. CREDIT: ELECTROHEAT. IGBT induction furnaces at the forefront. T he smelting process, once considered a traditional and resource-intensive method, has now undergone a remarkable revolution, transforming …
Role of Fire Assay. Fire assay is the traditional and most common method for refining gold. This process involves heating the gold in a crucible to a high temperature, causing it to melt and separate from any other metals that may be present. The gold is then poured into a mold and allowed to cool, forming a solid bar.
Red Chris Mine. Location: 80 kilometres south of Dease Lake, B.C. Mine type: Open pit. Commodities: Copper, gold. Owner: Imperial Metals. Projected mine life: 2043. The Red Chris Mine was acquired by Imperial Metals in 2007, and the company has invested in the project significantly over the years.
Ores that contain copper in the U.S. are typically mined in large, open-pits. Copper processing facilities are usually located near mining or extraction sites. Significant waste volumes are associated with copper production. Mine wastes may contain radionuclides due to their natural presence in ores and can be a source of TENORM.
حقوق النشر © 2024.Artom كل الحقوق محفوظة.خريطة الموقع