CFD modeling of MPS coal mill with moisture evaporation
Coal pulverizers play an important role in the functioning and performance of a PC-fired boiler. The main functions of a pulverizer are crushing, drying and separating the fine coal particles toward combustion in the furnace. It is a common experience that mill outlet pipes have unequal coal flow in each pipe and contain some coarse particles.
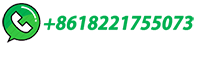