Tailoring materials by high-energy ball milling: TiO2 …
High-energy ball milling was carried out in a planetary ball mill (Fritsch Pulverisette 6) provided with an 80 cm 3 WC vial and 15 mm WC balls. The ball to powder mass ratio (BPR) was fixed at 35:1 and milling was done under air at rotational speeds of 350 and 500 rpm. Process was performed for several time periods from 5 to 360 min of ...
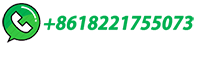