Revolution of Grinding Mill (Roller Body), Design, …
Common parts of a Roller Body. 1. Break roll feed box. 2. Feed inlet. 3. Middle wall. 4. Impulse transmitter. 5. Feed gate segment. 6. Feeding device. 7. Break feed roll
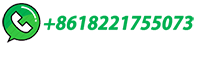
Common parts of a Roller Body. 1. Break roll feed box. 2. Feed inlet. 3. Middle wall. 4. Impulse transmitter. 5. Feed gate segment. 6. Feeding device. 7. Break feed roll
Roller mill advantages Now that we understand the basic principles of operation, there are four main advantages that direct people to use a roller mill rather than a hammer-mill, …
Rolling mills always use a minimum of two rollers, regardless of the number of rollers used. A set of rotating rollers grips the material and propels it forward as it moves through the process. After that, the material is forced …
The high pressure roller mill is the same as the roller crusher in that there are two working rollers, but the working principles of the two are different. The high pressure roller mill is mainly composed of frame, extrusion roller, transmission device and feeding device. The squeezing roller is composed of a movable squeezing roller and a ...
The principle of roller milling is the gradual reduction of grain by breaking it open and reducing the particle size between successive pairs of rolls. At every stage …
The breakage equation for roller milling of wheat kernels in terms of the size of the input and output particles is given in its cumulative form by (1) P 2 (x) = ∫ D = 0 D = ∞ B (x, D) ρ 1 (D) d D where ρ 1 (D) is the particle size distribution of the feed entering the roller mill, P 2 (x) the cumulative particle size distribution of the ...
The MPS vertical roller mill - built to last, reliable and energy-efficient - is the optimum solution when it comes to performing several process steps in one unit. Advantages of the MPS vertical mill . ... Working principle. Three stationary grinding rollers roll on a rotating grinding table. The material is drawn in between the rollers and ...
What is the Principle of three roll mill? The three roll mill has 6 main parts, such as roller, bearing, motor, heating dealing, cast parts and painting. The motor drives cast gears, to move 6 pcs of bearings of rollers. The cooling system controls the water of each roller, temperature is cannot be belittled. If higher temperature, you may have ...
2. Rolling Cluster Mill: ( Types of Rolling Mills ) A rolling mill with four levels is known as a cluster rolling mill. Each of the two working rolls within this rolling mill is backed by two or bigger backup rollers that can roll rigid materials. Rolls with a minor diameter but a very long length may be required to get the effect sought.
Operating Principle. Roller mills consist of a series of rollers that are mounted on a frame, spinning on bearings. The material to be processed is fed into the roller mill, and as the rollers rotate, they crush or grind the material into smaller particles. The grind size is set by adjusting the gap between the rollers.
The vertical roller mill (VRM) is a type of grinding machine for raw material processing and cement grinding in the cement manufacturing process.In recent years, the VRM cement mill has been equipped in more and more cement plants around the world because of its features like high energy efficiency, low pollutant generation, small floor area, etc.. The …
Rolling is the most important metal forming process. More than 95% of ferrous and non-ferrous metals and alloys are processed to their usable shapes by rolling. Usable shapes of rolled metals are plate, sheet, strip, foil, different sections like rail, beam, channel, angle, bar, rod, and seamless pipe, etc., as shown in Fig. 1.1 and Fig. 1.2.
The design and working principle or operation principle of the mill are shown here in an animation. In particular vibrations in the grinding plant are of crucial importance. The using of reinforced concrete pylons for the …
Along with roller mills, disc mills are the main types of grinders used for milling grains of wheat, maize, and other crops. Product grain size typically ranges from 300 to 200 µm. ... The principle of action of a ball mill is as follows. A rather large number of grinding bodies and the material being ground are placed inside a cylinder ...
PRINCIPLE OF OPERATION Our flagship pendulum roller mills are equipped with three pendulum roll assemblies suspended from a rotating carrier. As the carrier rotates, centrifugal force causes the roll assemblies to swing outward against the stationary ring. Plows direct material from the mill floor to the grinding zone
Call (314) 621-3348, email us at info@williamscrusher, or locate an agent near you. Williams Patent Crusher is an industry-leading roller mill manufacturer. Learn about our vertical roller mills, centrifugal roller mills and more.
Abstract. Vertical roller mills (VRM) have found applications mostly in cement grinding operations where they were used in raw meal and finish grinding stages and in power plants for coal grinding. The mill combines crushing, grinding, classification and if necessary drying operations in one unit and enables to decrease number of equipment in ...
Unlike three high roller mills, the metal sheet will pass through only once. If you want to further reduce the sheet thickness, you need to take out the sheet from the machine and feed it again. In this rolling machine, the top and bottom rollers are the main rollers, whereas the middle rollers are just backup rollers ( Green Color in the picture).
Following are the 6 different types of rolling mills used in many industries: Two high rolling mills. Three high rolling mills. Four high rolling mills. Cluster rolling mills. Planetary rolling mills. Tendem or …
The roller mills increased the capacities of flour mills, as well as amount, diversity and quality of flour and speed up the milling process compared to millstone ground operation. ... the gradual reduction system whose main features were the use a large number of process stages and exclusive use of roller mills for grinding. The principle of ...
Rolling is a metal forming process in which the deformation takes place under the application of Compressive forces between the rollers. In this article, we are going to discuss a detailed presentation on the Rolling Process with its Principle, Working, Types of Rolling Mills, Advantages, Disadvantages & Applications.
Roller mills use the process of stress (which is applied by the rotating wheels) and attrition in milling of solids in suspensions, pastes or ointments, and some …
The working principle of the roller mill is mainly divided into two steps: 1. The material first enters the center of the grinding wheel through the feeding hopper, and is then ground into fine powder by the grinding wheel. During this process, grinding wheels are usually made of high hardness wear-resistant materials to ensure long-term use ...
How many rollers are used in a rolling mill? The quantity of rollers employed in a rolling mill varies based on the specific application and the desired final product. Rolling mills can have two to several dozen rollers arranged in a specific configuration. Common roller configurations include two-high, three-high, four-high, and …
Because the roller press and the ball mill are two completely independent circulation systems, they are easier to operate and control and are more energy-saving. ... Working Principle Of Cement Roller Press. The …
The roller mill's ability to reduce materials to a uniform particle size provides more control of product characteristics and minimizes waste, as shown in Figure 1. The …
Summary: Vertical roller mill is a type of grinder used to grind materials, we can supply LM and LUM series vertical roller mill, Detail overview about vertical roller mill working principle in PDF, welcome to preview and download. LM Vertical Grinding Mill Working Principle. The grinding plate rotates under the action of main motor of LM …
Construction of Edge Runner Mill: The basic parts of this mill consist of two heavy rollers and a bed made of stones or granite which is used for the grinding of the materials, Fig.1. The rollers are mounted on the central horizontal shaft and move around the bed in a shallow circular pan. Working of Edge Runner Mill:
David O'Connell, director of scientific affairs at PCI Pharma Services, discusses the principles of roller compaction – particularly in the development and manufacturing of solid oral dosage forms containing highly potent active pharmaceutical ingred. ... such as an oscillating mill. The purpose of dry granulation is to increase the …
A triple roller mill consists of three rollers of equal diameters and is made up of hard abrasion-resistant material (stainless steel usually). These rollers are arranged parallelly and are horizontally fixed to a rigid frame. The pressure and gap between the rollers can be adjusted. A hopper is fixed between the first two rollers, and the last ...
حقوق النشر © 2024.Artom كل الحقوق محفوظة.خريطة الموقع