BENEFICIATION OF LOW-GRADE IRON ORES
In order to process such reserves in an economically viable project at Kanjamalai'(2 million tonnes per annum) iri~Salem fashion, efficient technologies are essential. Tocope with the district and Kavuthimalai (1 million tonnes per annum) of ... ore ispnisent as banded iron orefoflT1ationsY!!th.fecont~nt,. atfinersize.d) alumina t~ silica ratio ...
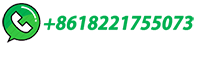