What is mineral dressing or ore beneficiation?
Published Dec 12, 2019. + Follow. The first process most ores undergo after they leave the mine is mineral dressing (processing), also called ore preparation, and ore dressing or ore beneficiation ...
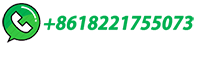
Published Dec 12, 2019. + Follow. The first process most ores undergo after they leave the mine is mineral dressing (processing), also called ore preparation, and ore dressing or ore beneficiation ...
Mining Surface Arrangements: Ore Dressing and Milling, Sampling Ores, Roasting Ores, The Cyanide Process [Company, Colliery Engineer, Jackson, Kerby] on Amazon. *FREE* shipping on qualifying offers. Mining Surface Arrangements: Ore Dressing and Milling, Sampling Ores, Roasting Ores, The Cyanide Process
This paper describes the commercial implementation of HPGR in tertiary crushing followed by a tower mill at a copper–lead–zinc ore dressing plant, focusing on the operational parameters and separation performance. The paper then discusses several challenges in design and operation and presents the outlook for the technology. 2.
Mineral processing, also known as ore dressing, mineral beneficiation, or mineral engineering, is defined as the science and art of separating valuable metallic and …
The control of a milling operation is a problem in imponderables: from the moment that the ore drops into the mill scoop the process becomes continuous, and continuity ceases only when the products finally come to rest at the concentrate bins and on the tailing dams. Material in process often cannot be weighed without a ...
The ore lumps from the mines have the lump size of 10 - 100 cm while the individual minerals have grain sizes below 0.1 mm. Hence, the first step in any ore dressing plant is to aim at liberation by size reduction or comminution. Comminution of any ore is carried out in several stages using different crushing equipments.
In addition, the influence of ore blending on ore dressing is reported in some of the research [10, 12, 14,32]. It is difficult to treat the ore blending target as a constraint to meet the ...
Mineralogy applied to ore dressing is a reliable guide for designing and operating an efficient concentrator. A procedure for conducting mineralogical studies in conjunction …
The Central Mine (Vostochny Mining and Ore-Dressing Combine) is a uranium mine in Ukraine. It is currently in operation. Empower your strategies with our Central Mine (Vostochny Mining and Ore-Dressing Combine) report and make more profitable business decisions. Note: This is an on-demand report that will be delivered …
Classification is the process of separating par ticles by size into two or more products acco rding to. their behavior in air or water (liquids). 2.2 The Classification methods are o f two types ...
Development of scientific and experimental basis for dry processing (milling) of different ore minerals is one of the promising directions of ore pre-treatment which helps save money and energy [1, 2].Impact fracture is most feasible prior to ore dressing, this method has advantages in fracture extent, energy intensity and disclosure …
An intelligent integrated method is proposed for optimizing the head grade and dressing grade in the mining and ore-dressing management of metal mines, beginning with the establishment of a nonlinear constrained optimization model with the objective function of economic benefit, two constraints comprising of the resource …
Ball Mills. In all ore dressing and milling Operations, including flotation, cyanidation, gravity concentration, and amalgamation, the Working Principle is to crush and grind, often with rod mill or ball mill, the ore in order to liberate the minerals. In the chemical and process industries, grinding is an important step in preparing raw ...
Figure 8.2.1 Simplified Schematic of an Underground Mine. A shaft is a vertical mine opening, a level is horizontal and a decline is sloped so as to allow passage by wheeled vehicles. Figure 8.2.2 Underground at the Myra Falls Mine, Vancouver Island. A typical ore body will contain a few percent of ore minerals—typically sulphide minerals ...
mineral processing, or ore dressing, Mechanical treatment of crude ores to separate the valuable mineral s. Mineral processing was at first applied only to ores of precious metals but later came to be used to recover other metals and nonmetallic minerals. It is also used during coal preparation to enrich the value of raw coal.
Ball Mill Ball mill is ore dressing equipment, mainly used for crushing bulk ore materials into ore pulp, for further separating operations.; Spiral Classifier Spiral separator is large grading equipment. This machine classifies materials according to the different sizes and proportions of solid particles. Magnetic Separator Magnetic separator is common used …
Ore Mining and Dressing Preliminary Study Report (pdf) (623.5 KB, September 2011, 820-R-10-025) Review of wastewater discharges from active ore mines that produce copper, lead, zinc, gold, silver and molybdenum. Findings are used to support determination whether to revise existing Effluent Guidelines regulations at 40 CFR Part …
Mining historian Kerby Jackson introduces us to a work on ore processing in this important re-issue of "Surface Arrangements: Ore Dressing and Milling, Sampling Ores, Roasting Ores, The Cyanide Process". Unavailable since 1899, this publication offers rare insights into all the major subjects related to milling and processing precious metal ores. ...
A Textbook on Mining Engineering: Preliminary Operations at Metal Mines, Metal Mining, Surface Arrangements at Metal Mines, Ore Dressing and Milling (Classic Reprint) [International Correspondence Schools] on Amazon. *FREE* shipping on qualifying offers.
The Chilean Mill consists essentially of four heavy cast iron rollers with convex surfaces which are rotated on a concave surfaced die ring. The purpose of this design is to keep the ore between the crushing surfaces at all times, thus avoiding the necessity of scrapers to direct the ore into the crushing areas, and also to avoid spillage.
Mineral Processing. Mineral processing is the process in which chemical or physical methods are used to separate the useful minerals in the ore from the useless minerals (usually called gangue) or hazardous minerals, or to separate multiple useful minerals. In the early years, mineral processing was called mineral concentration or …
Contribute to yunan88/crusher development by creating an account on GitHub.
Contribute to dihog/sbm development by creating an account on GitHub.
Journal of Mining Science. Article. Features of Ore Disintegration in Dry-Milling Centrifugal Breaking Machine of a New Design. MINERAL DRESSING. …
Contribute to jgw2023/sbm development by creating an account on GitHub.
beneficiation. particle separation. bulk oil process. flotation, in mineral processing, method used to separate and concentrate ores by altering their surfaces to a hydrophobic or hydrophilic condition—that is, the surfaces …
Extraction processes include dressing (picking, sorting, washing of ores), milling (crushing, grinding, etc.) and beneficiation (processing to improve purity/quality). Wastewater is generated during the mining process from groundwater produced during ore extraction, from water used by operators for equipment cooling and dust control, and …
DOI: 10.1038/114856a0. Corpus ID: 4104868. Ore Dressing: Principles and Practice. C. D. Materials Science. Nature. TEXT-BOOKS of ore dressing are frequently little more than …
The theory and practice of ore dressing (McGraw-Hill Book Co., 1915), by Edward S. Wiard (page images at HathiTrust) Handbook of milling details (McGraw-Hill Book Company, 1914) (page images at HathiTrust)
mineral processing, art of treating crude ores and mineral products in order to separate the valuable minerals from the waste rock, or gangue. It is the first process that most ores undergo after mining in order to provide a …
After the coarse ore has been extracted, it is crushed directly at the deposits with the aid of cone crushers or jaw crushers to more manageable sizes of approx. 15 mm. This is also known as lump ore. In addition to lump ore, fine ore (approx. 1 mm) and ground ore (ore powder) (approx. <0.1 mm) can also be obtained by crushing and grinding.
حقوق النشر © 2024.Artom كل الحقوق محفوظة.خريطة الموقع