Ball Mill Operation -Grinding Circuit Startup
Normal Shutdown Sequence of Ball Mill and Grinding Circuit. Shut off cyanide metering pump. Put weight controller into MANUAL mode and turn controller output to 0%. Run the ball mill for 15 …
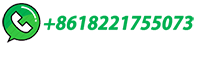
Normal Shutdown Sequence of Ball Mill and Grinding Circuit. Shut off cyanide metering pump. Put weight controller into MANUAL mode and turn controller output to 0%. Run the ball mill for 15 …
Design and Analysis of Ball Mill For Paint Industries Mayur H Patel1 Mr. Vishal A Pandya 2 1ME-Machine Design- pursuing2Asst. Prof 12 B.V.M Engineering College, ... feeding force, and enter the next procedure. III. TYPES OF BALL MILL Ball mills are used for grinding things down or for mixing things up. They grind ores down to powders before ...
Small Ball Mill Capacity & Sizing Table Ball Mill Design/Power Calculation Skip to content Laboratory Testing Consulting & Engineering Process Equipment
the milling process takes place during rotation as a result of the transfer of kinetic energy of the moving grinding media into the grinding product. The design of a ball mill can vary significantly depending on the size, the equipment used to load the starting material (feeders), and the system for discharging the output product.
Type CHRK is designed for primary autogenous grinding, where the large feed opening requires a hydrostatic trunnion shoe bearing. Small and batch grinding mills, with a diameter of 700 mm and more, are available. These mills are of a special design and described on special request by all Ball Mill Manufacturers.
Ball mills are commonly used for crushing and grinding the materials into an extremely fine form. The ball mill contains a hollow cylindrical shell that rotates about its axis. This …
Scale-up procedure for continuous grinding mill design using population balance models . × ... 1969) grinding in laboratory-scale ball mills and is, therefore, a promising candidate for ball mill scale-up design. The development of the equations required for scale-up design is sketched below (Herbst et al., 1971a). The linear, size-discretized ...
The ball mill process parameters discussed in this study are ball to powder weight ratio, ball mill working capacity and ball mill speed. As Taguchi array, also known as orthogonal array design, adds a new dimension to conventional experimental design, therefore, Orthogonal array (L9) was carefully chosen for experimental design to …
884/463 = 1.91. 3.05 x 1.91 – 5.83 meters (19.1 feet) Therefore, use one 3.05 meter (10.0 foot) diameter inside shell 2.89 meter (9.5 foot) diameter inside new liners by 5.79 meter (19.0 foot) long overflow ball mill with a 40 percent by volume ball charge. For rubber liners add 10% or 0.58 meters (approximately 2 feet) to the length.
IV. BALL MILLS Ball mills are one of the more common mills and use a closed cylindrical container that is rotated horizontally on its axis so that the media cascades. A typical ball mill has an L/D ratio of 1.5:1. Ball mills are filled with spheres or other shapes made of steel or ceramics; or with pebbles made of flint (or of an ore being ground).
atory ball mill, but it requires a reference sample ore for which wi is known. In the Berry and Bruce procedure, 2 kg weight samples of the reference and unknown ores with a par‐ ticle size under 1.651 mm are wet ground in a laboratory ball mill that is 305 mm in diam‐
This Grindability Test or Bond Ball Mill Work Index Procedure is used to determine the Bond Work Index of minus six mesh or finer feed ore samples. These equation application methods are used to …
Rod Mill Design Calculations. EF1 – Dry Grinding – for the same range of work, dry grinding requires 1.3 times as much power as wet grinding. EF2 – Open Circuit Grinding – when grinding in open circuit ball mills, the amount of extra power required, compared to closed circuit ball milling, is a function of the degree of control required ...
Ball Mill & Rod Mill Design. In all ore dressing and milling processes, including flotation, cyanidation, gravity concentration, and amalgamation, it is necessary to crush and grind, often with rob mill & ball mills, the ore in order to liberate the minerals. In the chemical and process industries, grinding is an important step in preparing raw ...
In this article, the four main application areas of Retsch laboratory ball mills in battery technology will be outlined. Each area can be categorized under specific application examples: Section 1: Reduction of the material particle size in batteries. Section 2: Mixing and coating of particles.
26600 Pekan, Pahang, Malaysia, Phone: +6094246255; Fax: +6094246222. *. Email: [email protected]. ABSTRACT. This project is to design and fabricate the mini ball mill that can grind the solid ...
The ball milling design significantly depends on the size of mill jar, required particle size distribution of powder and grinding media (balls) [13], [14], [15]. The main purpose of milling process is to obtain required particle size of the powder without any contamination, increasing the output of the milling circuit and overall reduction in ...
Ball Mill Design Parameters. Size rated as diameter x length. Feed System. One hopper feed; Diameter 40 – 100 cm at 30 ° to 60 ° Top of feed hopper at least 1.5 meter above the center line of the mill.
Bakota, John F. (1977). "Mill Building Design Procedure," Engineering Journal, American Institute of Steel Construction, Vol. 14, pp. 130-137. The design of an industrial mill building involves myriad assumptions and parameters. In the current state of the art, there is disagreement about the validity of many of these assumptions and parameters.
Taguchi-based experimental design technique has been a major research area for making systematic approaches to understand the complex process of ball mill …
The basic parameters used in ball mill design (power calculations), rod mill or any tumbling mill sizing are; material to be ground, characteristics, Bond Work …
Demerits: 1. High Energy Consumption: Ball mills often require high energy input for the grinding process, making them less energy-efficient compared to some other milling techniques. 2. Wear and Tear: The grinding media and liners experience wear, requiring regular maintenance and replacement. 3.
Ball Mill Sole Plate. This crown should be between .002″ and . 003″, per foot of length of sole plate. For example, if the sole plate is about 8′ long, the crown should be between .016″ and .024″. Ball Mill …
This paper presents the development of a mill scale-up procedure based on population balance models of grinding circuits. Models containing various degrees of details in their representation of the kinetics of breakage, material transport through the mill, and performance of the classifier are examined; and the extent to which each may be …
Ball Mills. In all ore dressing and milling Operations, including flotation, cyanidation, gravity concentration, and amalgamation, the Working Principle is to crush and grind, often with rod mill or ball mill, the ore in order to liberate the minerals. In the chemical and process industries, grinding is an important step in preparing raw ...
mathematical model, grinding machining process, cutting experiment of ball end mills, and the calculation for a ball end mill, a ball end mill parametric design system is built by …
Planetary Ball Mills 101 from Union Process Inc. Planetary ball mills share the same design as other basic ball mills – a grinding jar filled with media and rotated on its own axis. But their unique design takes advantage of centrifugal force and the Coriolis effect to grind materials to a very fine or even micron size. These forces come into ...
A pharmaceutical ball mill is a type of grinder used to grind and blend materials while manufacturing various dosage forms. The size reduction is done by impact as the balls drop from near the top of the shell. Ball mills are used primarily for single-stage fine grinding, regrinding, and as the second stage in two-stage grinding circuits.
This work aims to design a simple horizontal ball mill. Calcium carbonate material from limestone and eggshells powder was ground using the developed ball …
Chemistry Process Design and Development, 12 (2), 121-129. 25. ... To fabricate this ball mill, we first design a model using Solidwork and checked for interferences. Then, we start looking for ...
حقوق النشر © 2024.Artom كل الحقوق محفوظة.خريطة الموقع