Construction Working and Maintenance of Crushers for …
crusher for another pass through the machine. Efficiency of a multiple stage crushing plant can be maximized by operating a primary crusher at a setting which produces a satisfactory feed size for the secondary crusher and operating the secondary crusher (or the last stage crusher) in a closed circuit. Glossary of Terms
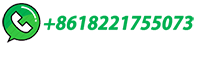