Separation and purification technologies for lactic acid – …
Data from the industrial recovery process are limited in open sources. Ecochem Inc., a Du Pont–Conagra partnership, had developed a recovery and purification process that produced a by-product ammonium salt instead of insoluble gypsum cake, and the company intended to sell this as a low-cost fertilizer (Datta and Henry 2006).
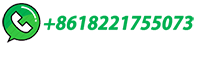