Arizona Copper Milling LLC
Services Processing Ores for Established Operations We process copper ores from established operators in the region in exchange for a processing and tailings disposal fees. Our copper ore processing service is consistent with Arizona's ESG policies as it is intended to serve multiple operators and thus conducive to a rational use of water …
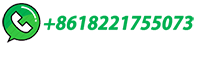