Cement Grinding
Water Spray in Cement Mills. Water spray installed generally in second compartment of ball mill to control cement temperature. Cement discharge temperature should be kept below about 110 o C but, the same time should allow some 60% dehydration of gypsum to optimize cement strength without excessive false set.
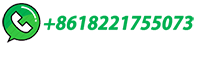