Principles of Grinding in Ball Mills
The most desirable angle to accomplish this falls between 50 to 60° from horizontal. The lower end of this range applies to wet grinding applications for soft materials. The higher break point is reserved for harder wet grinding materials such as enamel as well as dry materials. This angle of break is also determinate upon the size of the mill.
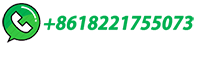