Advantages of Ball Milling
Ball mills have a number of advantages for milling solids either wet or dry. In order to minimize product contamination, ball mills can be constructed with a wide range of materials including abrasion-resistant high-chrome steel, alumina brick, and cast polyurethane. Because all of the solids in a ball mill are forced to endure thousands of ...
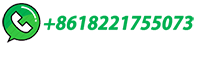