Variables in Ball Mill Operation | Paul O. Abbe®
A Slice Mill is the same diameter as the production mill but shorter in length. Request Price Quote. Click to request a ball mill quote online or call 630-350-3012 to speak with an expert at Paul O. Abbe® to help you determine which design and size ball mill would be best for your process. See our Size Reduction Options.
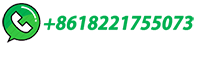