Pulverizers 101: Part I
Our experience with both RP and MPS pulverizers has been that mills designed for a throughput of about 120,000 pounds of coal per hour, an HGI of about 45 to 50, and coal fineness exceeding 75% ...
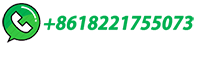
Our experience with both RP and MPS pulverizers has been that mills designed for a throughput of about 120,000 pounds of coal per hour, an HGI of about 45 to 50, and coal fineness exceeding 75% ...
On the basis of the above model, Zeng et al. considered the impact of the moisture of raw coal on the energy balance of coal mills and established a nonlinear dynamic model of coal mills; although the model's outputs are consistent with the actual outputs, the problem of having to identify many parameters remains [8]. Coal mills are …
Next, the paper estimates the coal outlet mass flow of the coal mill by using extended Kalman filter (EKF), and the result is compared with the coal flow instruction. Finally, we take the estimation of coal outlet mass flow as the new controlled variable and use inferential predictive control method to solve the coal mill control problems. The ...
Sulfur in the form of pyrite (FeS 2) can lead to spontaneous combustion and contributes to the abrasion in coal mills; therefore, if a lower quality coal containing pyrite is used in place of the design coal it can lead to problems.
A non-detected fault in a coal mill results in problems controlling the coal flow to the furnace, under unfortunately operating conditions, it can result in too much coal to the furnace resulting in an overheating of the furnace and thereby the plant. To detect faults in a system such as the coal mill, a number of different approaches can be ...
A potentially serious problem exists if coal dust is allowed to accumulate inside a building or enclosure, for example around an unloading facility or because of a leaking coal conveying line. ... Coal mill hot air inlet temperatures should never be more than 600 F and the outlet temperature should not exceed 200°F on Raymond coal mills. If ...
Addressing a problem first identified 50 years ago, federal regulators say stricter new rules to limit miners' exposure to silica dust are expected to finally go on the …
2.2.1 Conceptual Framework for Output of Double-in and Double-out Ball Mills. One of the important links in establishing a system dynamic model is to draw the cause and effect diagram of. the ...
Introduction. This article concerns itself with vertical grinding mills used for coal pulverization only ( coal pulverizers ), although vertical grinding mills can -and are- used for other purposes. The 3D model in the saVRee database represents a vertical grinding bowl mill. Other grinding mill types include the ball tube mill, hammer mill ...
The coal mill is one of the important auxiliary engines in the coal-fired power station. Its operation status is directly related to the safe and steady operation of the units. In this paper, a ...
The source of the problem is the coal pulveriser mills not being able to produce the more stringent fineness required. This results in coal/char particles burning higher up in the furnace, causing excessive reheater temperatures, etc. One could attempt to increase the rotational speed of the vertical spindle mills by at least 15%.
We have found that targeting an A/F ratio around 1.8 lb of air per lb of fuel is best. For some pulverizer types, such as ball tube mills and high-speed attrition mills, often a 1.6 A/F ratio is ...
The coal mill can also grind petroleum coke and anthracite down to a fineness below 5% +90 micromillimeters (mm) when coupled with a variable speed mill motor. No sticky situations. The ATOX® Coal Mill can grind and dry raw coal with up to 25 percent moisture level. By adjusting the gas flow stream with the nozzle, you can deal with more ...
The coal mills are key equipments in the power plant, so it is important for unit's security and stable operation that condition monitoring and fault diagnosis should be applied in the coal mills. ... which combine the two methods together to solve not only the coal mill fault diagnosis fuzzy problem, but also the structure subjectivity ...
Through analyzing faults, we find that faults of the coal mills present characteristics of fuzzy and uncertain, which a kind of fault may exhibit a variety of …
We used a multi-channel (32 channel) data logger as scanner, which can scan a numbers of RTD / Thermocouple signal. As we have eight numbers (08) of coal mill and each coal mill has four outlet coal pipes, so we have to measure 32 numbers of coal pipe temperature. We design and procure 32 numbers of special type surface mounted RTD.
Fan et al., designed a knowledge-based fine-grained coal mill operator support/control system for coal plants. The system is composed of mathematical coal mill model and expert knowledge database and has the ability of parameter estimation, coal mill performance monitoring, fault diagnosis and prediction, early warning and problem …
Coal Mill Temperatures . Coal mill hot air inlet temperatures never be more than 600should F and the outlet temperature should not exceed 200°F on Raymond coal mills. If the flow of raw coal to the coal mill is interrupted for any reason (for example: plugging, failure of the coal feeder, etc.), the outlet temperature of the coal mill can ...
The present paper discusses an innovative means for solving the problem of accumulation of waste coal in some pulverized coal fired plants. A major waste in a pulverized coal fired power plant is the reject produced from pulverizing mills. When coal is ground in a bowl mill heavy mineral matters are separated, but they still contain a small …
YES. Our boiler mills and coal pulverizers span the globe and are built in a variety of sizes and capacities. We provide customized maintenance solutions, and offer a full spectrum of high-quality solutions for each—in addition to our thousands of standard boiler mill parts and boiler service solutions. This is the Power of Yes.
The ball mill is a traditional coal pulverizer machine, which has been widely used since it was invented. In the cement plant, the new dry process cement manufacturing requires the moisture content of coal powder to be 0.5% ~ 1.5%, while that of raw coal is 1.5% ~ 4.0%.
Coal Mill a.s. je moderní, rozvíjející se společnost, která disponuje špičkovou technologií na zpracování černého uhlí. Byla založena v říjnu 2006 a je zapsána v obchodním rejstříku vedeném Krajským soudem v Ostravě, oddíl B, vložka 3104. Areál firmy o rozloze 17 686 m2 je situován ve výrobně– průmyslové zóně ...
This report contains the results of a 16 month study to examine the problem of pulverizer outages and to identify root cause failure modes for the major mill types currently in service. A data base of 469 pulverizers, the majority larger than 40 tons/hr coal capacity, was compiled by surveying the utilities with coal fired boilers in this ...
is composed of mathematical coal mill model and expert knowledge database and has the ability of parameter estimation, coal mill performance monitoring, fault diagnosis and prediction, early warning and problem solving [5]. Wang et al., based on the coal mill model developed by Wei et al., proposed a method to monitor the state of …
Abstract. The present paper discusses an innovative means for solving the problem of accumulation of waste coal in some pulverized coal fired plants. A major waste in a pulverized coal fired power ...
To solve the problem of acquiring massive fault data, a method used for fault data generation is proposed in this paper, by which fault data samples can be generated by …
20. 13.1.Fineness Fineness is an indicator of the quality of the pulverizer action. Specifically, fineness is a measurement of the percentage of a coal sample that passes through a set of test sieves usually designated at 50, 100, and 200 mesh A 70% coal sample passing through a 200 mesh screen indicates optimum mill performance. …
Abstract. Aiming at the typical faults in the coal mills operation process, the kernel extreme learning machine diagnosis model based on variational model feature extraction and kernel principal …
Coal mills consume a huge amount of station service electricity power of a coal-fired power plant. ... With a background of 25 years in solving problems brought about by coal ash in large boiler ...
In India, where ambient temperatures in summers usually exceed 45°C, pulverized coal catches fire quite easily and is a major problem for cement plants. Pulverized coal goes from the coal mill to the hoppers, silos and fine coal dust is also collected in bag filters. In all of these processes, cement plants introduce inert gas to prevent fires.
حقوق النشر © 2024.Artom كل الحقوق محفوظة.خريطة الموقع