Introduction to Rolling Process
Rolling is the most important metal forming process. More than 95% of ferrous and non-ferrous metals and alloys are processed to their usable shapes by rolling. Usable shapes of rolled metals are plate, sheet, strip, foil, different sections like rail, beam, channel, angle, bar, rod, and seamless pipe, etc., as shown in Fig. 1.1 and Fig. 1.2.
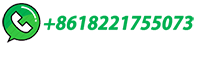