Iron Ore Processing, General
Making iron and steel from iron ore requires a long process of mining, crushing, separating, concentrating, mixing, agglomeration (sintering and pelletizing), and shipping …
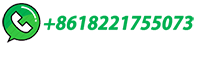
Making iron and steel from iron ore requires a long process of mining, crushing, separating, concentrating, mixing, agglomeration (sintering and pelletizing), and shipping …
Copper processing is a complicated process that begins with mining of the ore (less than 1% copper) and ends with sheets of 99.99% pure copper called cathodes, which will ultimately be made into products for …
regarding taconite iron ore processing. Taconite mining and processing fall under the North American Industry Classification System (NAICS) 21221 Iron Ore Mining. According to the 1997 Economic Census of Manufacturing, in 1997, 32 establishments owned by 26 companies produced products that are categorized in NAICS 21221 (U.S. Department of
Mineral Sampling. A. Gupta, D.S. Yan, in Mineral Processing Design and Operation, 2006 1.1. Iron ore was sampled before stock piling with a stacker. One hundred samples taken from the stacker-conveyor showed a standard deviation in the iron assay of ± 0.5 %. The ore assayed, on average, 59 % Fe.Sieve analysis of the samples showed that the …
Iron Ore Processing Flowsheet production line is a production of construction sand and stone dedicated production line equipment than traditional sand making energy savings of 50%. It can sand a ...
In the present study a detailed characterization followed by beneficiation of low grade iron ore was studied. The Run of Mine (R.O.M) sample assayed 21.91 % Fe, which is very low grade in nature.
Making iron and steel from iron ore requires a long process of mining, crushing, separating, concentrating, mixing, agglomeration (sintering and pelletizing), …
Iron ore processing operating practices vary depending upon the the quality of iron ore deposit. For high-grade ore, dry- or wet processing can carried out and for …
The process is simplified. The roasted ore is subject to magnetic separation after water quenching and classification. After magnetic separation, the magnetite fine powder with high iron grade, low arsenic and sulfur impurities is obtained. It is widely used for beneficiation of ores and waste residues containing weakly magnetic iron minerals.
Download scientific diagram | Simplified flow chart showing typical iron ore processing (Silva et al., 2021). from publication: Behavioural analysis of iron ore tailings through critical state ...
A fatty acid reagent combination was developed to float the specular hematite in a concentrate assaying over 65% iron. This same procedure and reagents are now being employed in present day operations. Crushing Hematite Rock. Three stage ore reduction is used with either a grizzly or vibrating screen between each crushing stage.
The iron ore fines sample was obtained from the Bellary-Hospet area, Karnataka, India for beneficiation studies. An iron ore sample of below 10 mm was used for this study. The sample consists of 56.0% Fe, 9.1% SiO 2 and 5.2% Al 2O 3. The sample was thoroughly mixed and appropriately sampled at different stages of processing
Nickel processing - Extraction, Refining, Alloying: The extraction of nickel from ore follows much the same route as copper, and indeed, in a number of cases, similar processes and equipment are used. The major differences in equipment are the use of higher-temperature refractories and the increased cooling required to accommodate the higher operating …
Activities involved in finding, mining and processing iron ore at our Pilbara operations have been simplified in the following diagram. Rio Tinto operates 11 iron ore mines in the Pilbara and the specific sequence of activities varies from mine to mine. Excellence in planning, scheduling and quality control are fundamental to the process.
Description. Mekanism adds various tiers of ore processing for better ingot yields from Silk Touch Ore. To acquire Silk Touch Ore the silk touch enchant needs to be enchanted on a pickaxe. Each tier use a specific machine to process the raw ore ( for direct ingots, dusts, clumps, shards or crystals ).Then the product is processed by the ...
Sintering is a thermal agglomeration process that is applied to a mixture of iron ore fines, recycled ironmaking products, fluxes, slag-forming agents, and solid fuel (coke). The purpose of the sintering process is manufacturing a product with the suitable characteristics (thermal, mechanical, physical and chemical) to be fed to the blast furnace.
An ironworks (or iron works) is an industrial plant for the production of steel from iron ores! Before the iron ores can be fed to the ironworks, they must first be mined (ore extraction) and specially processed for the blast furnace process (ore processing). These process steps are described in more detail in the following sections.
In all cases, the choice of reagents used will be based on the characteristics of the ore sample, and their cost and availability. For this reason, extensive laboratory and pilot …
Fig 3 Types of processing ores. The wet processing (Fig 4) is normally practiced for low / medium grade (60 % Fe to 63 % Fe) hematite iron ore. The wet process consists of multi-stage crushing followed by …
Iron ore sintering is the iron ore powder agglomeration process that changes fine iron ore powder into the lumpy iron-bearing raw material used for blast furnace ironmaking. High-temperature process and addition of alkaline flux will improve metallurgical performance of iron-bearing raw material. Besides, the sintering process …
Additionally, iron ore processing facilities often receive ores from various sources (such as satellite pits) with different qualities. These ores may be treated by different processing routes and/or blended to meet product specifications. Some examples of different iron ore crushing and screening flowsheets are provided below: 8.2.3.1.
Download scientific diagram | Flow chart of the mineral processing of hematite iron ore. from publication: An intelligent factory-wide optimal operation system for continuous production process ...
Platinum (element #78, symbol Pt) is a dense, silvery-gray metal. The platinum group of elements consists of metals with similar physical properties as platinum and these elements are among the rarest in the Earth's crust. They have high melting points, are dense or heavy and are non-reactive with other elements.
iron ore contain high sulfur, phosphorus Beneficiation. The common processes used to remove sulfur from iron ore concentrates are flotation and roasting. At the same time, the latter is costly and produces environmental pollution, so the main direction of research is to strengthen flotation. A large number of research results prove …
The blast furnace uses coke, iron ore and limestone to produce pig iron. Coal traditionally has been a key part of the coke-making process. The coal is crushed and ground into a powder and then charged into an oven where it is heated to approximately 1800°F in the absence of oxygen. As the oven is heated, the coal begins to melt so most of the ...
Iron ores are rocks and minerals from which metallic iron can be extracted. There are four main types of iron ore deposit: massive hematite, which is the most commonly mined, magnetite, titanomagnetite, and pisolitic ironstone. These ores vary in colour from dark grey, through to deep purple, rusty red and bright yellow.
The iron ore pelletizing process consists of three main steps: Pelletizing feed preparation and mixing: the raw material (iron ore concentrate, additives —anthracite, dolomite—and binders are prepared in terms of particle size and chemical specifications, dosed, and mixed together to feed the pelletizing process;
Abstract. Mining of iron ore is a highly capital- and energy-intensive process. Life cycle assessment (LCA) of the mining and mineral processing of iron ore in Australia was carried out in this chapter using SimaPro LCA software as a case study. The environmental impacts considered in the study were embodied energy and greenhouse …
In the open hearth process for producing steel, pig iron, steel scrap, and iron oxide in the form of iron ore or scale are melted in a Siemens-Martin open hearth furnace (Fig. 4.4), so called because the molten metal lies in a comparative shallow pool on the furnace bottom or hearth. The hearth is surrounded by a roof and walls of refractory ...
Home Technology Industry. Iron making. The primary objective of iron making is to release iron from chemical combination with oxygen, and, since the blast furnace is much the …
حقوق النشر © 2024.Artom كل الحقوق محفوظة.خريطة الموقع