Electroplating
Electroplating is the process of plating one metal onto another by hydrolysis, most commonly for decorative purposes or to prevent corrosion of a metal. There are also specific types of electroplating such as copper plating, silver plating, and chromium plating. Electroplating allows manufacturers to use inexpensive metals …
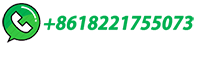