mining
Generally, the surface mining process includes first identifying the ore and waste rock, then removing the surface soil and debris, then drilling and blasting the ore and waste, removing the ore to processing facilities and …
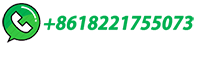
Generally, the surface mining process includes first identifying the ore and waste rock, then removing the surface soil and debris, then drilling and blasting the ore and waste, removing the ore to processing facilities and …
Abstract. The state-of-the-art blasting methodologies have been developed over the years to overcome the challenges of underground mining. The major challenges associated with Indian underground mines include ore dilution and narrow vein mining. The productivity enhancement from underground is another challenge, as most of the shallow …
Download scientific diagram | Drilling and blasting, loading and primary crushing operating costs as functions of P80 for (a) CE and (b) JC. from publication: A Mine-to-Crusher Model to Minimize ...
Contribute to naicha22/2022 development by creating an account on GitHub.
In this paper, the blasting parameters are designed based on the drilling data of the exploration geological stage, the geophysical and mechanical parameters of the mining area, and the geological ...
The first step in the mining and processing of nearly any mineral ore is comminution. Since the oil embargo of 1979, the mining companies have been striving to reduce energy ...
increase and better quantify data obtained dur ing drilling, and integ rate the data collected dur ing drilling into an analysis tool that can be used to help optimiz e subsequent dr illing and b lasting. Specifically, the three technical targets are development and implementation of: 1) a prototype measurements-while-drilling
n Preventing oversized rocks from entering the primary crusher to decrease the number of bridging incidents and hence downtime of the crusher. ... Data from ShovelCam was used to increase the fragmentation of the blast by tightening the drill pattern. Top size in the ROM ore muck-pile reduced from 1.2 m to 800 mm while 80% …
The emission of gas from the coal seams is one of the most important issues during the underground coal mining operation. Each year, coal gas emission from the underground stopes leads to the death of a large number of miners and is one of the biggest threats to workplace safety. In addition, ventilating and releasing coal gas outside of the …
iron ore primary crusher price. Shanghai Shibang Machine Co., Ltd. is a high technology, engineering group. We are specializing in the research, development, and …
The drilling pattern was changed. Changing the drilling diameter was found to be an inconvenience by the miners, since the tools used could not be modified without capital investment unavailable to them. Therefore, the drilling diameter was kept at 1 "1/2 (38.1 mm) and the explosive agents were kept the same.
Drilling and blasting are fundamental operations in the mining cycle and constitute an important component of the mining costs. Rock fragmentation can in principle be …
Abstract. The fundamental principles of rock fragmentation by crushing, blasting, and drilling are not well understood; however, empirical observations have provided means for predicting the energy requirements for these processes. Experimental procedures and methods of analysis used in comminution studies are described in this review.
Blasting plays a key role in mining operations, and its results can directly affect downstream operations, including crushing and milling. Therefore, predicting a …
If a spherical charge is buried in an infinite-depth homogeneous rock mass for blasting, the rock mass around the charge will bear different blasting actions and show different crushing characteristics due to different distances from the center of the charge (Fig. 1).The rock mass directly in contact with the charge will be impacted and …
Drilling is the first stage of open pit mining that has a considerable effect on the other stages of mining, including blasting, loading, hauling and crushing. An unsuitable drilling pattern may ...
In primary-secondary mining sequence, blast vibrations are induced in CRF during the extraction of adjacent stopes. Higher magnitude of blast vibrations may destabilize CRF causing failure and ...
The purpose of the primary crusher is to reduce the ROM ore to a size amenable for feeding the secondary crusher or the SAG mill grinding circuit. The ratio of reduction through a primary crusher can be up to about 8:1. Feed: ROM up to 1.5 m. Product: -300mm (for transport) to -200mm (for SAG mill) Feed Rate:
By using a 1.6 m drill, it is possible to provide 1.3 m advance in theory with the classic single V-cut blasting pattern. In order to make more advance, it is necessary to switch to the double V ...
Auger drilling is the simplest form of drilling. It involves the manual rotation of a helical screw into the ground, usually by two people although auger drills can also be mounted to small vehicles. Once the auger drill is deep enough, the earth is lifted up by the blade of the screw. This kind of drill specializes as an initial geochemical ...
A typical example of a 3-D model of a surface mine is shown in Figure 5. Typically, sets of parameters associated with blasting pattern include: bench height, hole diameter, hole depth, burden ...
TACONITE MINING Taconite mining and processing is very costly due to the hardness and abrasiveness of these low grade iron ores. The processing usually involves two stages of crushing and coarse and fine grinding after primary crushing, and the comminution costs per tonne will increase substantially for each downstream stage.
The people who work in mines are called miners. People dig mines to get such things as diamonds, coal, silver, salt, and many other materials. When a mine provides stone for …
Drill and blast supervisors. Managers. Procurement officers. People related to mine production. For further information contact: Head of Conferencing, Jackie van der Westhuizen SAIMM, P O Box 61127, Marshalltown 2107 Tel: (011) 834-1273/7 · Fax: (011) 833-8156 or (011) 838-5923 E-mail:[email protected] · Website: …
Selecting the right crusher. Jaw crushers are the most common solution in underground applications when the throughput is less than 1,000 tons per hour, depending somewhat on the scalping solutions. Above 1,000 tph, primary gyratory crushers begin to look interesting, and after the throughput reaches 2,000 tph, jaw crushers are very rare, …
Blasting and Mining Performance. Drilling and blasting parameters have a direct impact on mine pro duction levels. Ac-. cordingly, one of the parameters that should be optimized is the diameter of ...
Drilling and blasting are the two most significant operations in open pit mines that play a crucial role in downstream stages. While previous research has focused on optimizing these operations as two separate parts or merely in a specific parameter, this paper proposes a system dynamic model (SDM) for drilling and blasting operations as …
The results show that energy consumption at the primary crusher is a sum of two components: energy directly involved in crushing the rock, and additional energy used for winning the inertial ...
You've already forked sbm 0 Code Issues Pull Requests Packages Projects Releases Wiki Activity
The maximum crushing ratio of coarse crushing is about three. The main force in the coarse crushing of ore is crushing. Typical coarse crushing equipment includes jaw crusher, gyratory crusher, and roller-tooth crusher. Ore medium crushing is a process of crushing ore blocks with a feeding particle size of 125–400 mm to 50–100 mm.
حقوق النشر © 2024.Artom كل الحقوق محفوظة.خريطة الموقع