Machining 101: What is Grinding? | Modern Machine Shop
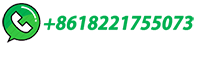
A combination sine plate and magnetic chuck used to grind precision angles that is set up just like an ordinary sine plate but has its own permanent magnet to hold the work. A device that can be used to hold a workpiece at a 45-degree angle and extend the magnetism of a magnetic chuck to the workpiece. Study with Quizlet and memorize flashcards ...
It is also known as the Abrasive Grinding Machining Process. Why Abrasive Grinding Machining Process? Because the abrasives are placed on the surface to do the finishing process with …
Watching important parameters allows you to improve profitability by making necessary changes. Before getting into the four categories that influence grinding efficiency, it's important to know how the grinding process works. When you're using a grinding machine, three interactions are happening at the same time: cutting, plowing …
Cryogenic grinding is most effective when the product is sprayed with liquid nitrogen as it is being conveyed and introduced into the Attritor. An additional benefit of cryogenic milling in an internally agitated ball mill is the ability to fully immerse the product in liquid nitrogen during milling. The level of liquid nitrogen in the milling ...
Grinding is a unit operation that reduces solid matter into smaller particles. Define grinding process: Grinding is a processing method that uses abrasives to remove material. The process of removing material with abrasives is one of the earliest production techniques used by humans. Grinding process is a micro-processing method.
Cement grinding is the last step of cement making. The main grinding equipment cement mills grind the clinker to finished cement powders. Material – batching – Cement Mill – cement packing – bulk loading. In …
A grinder is commonly used to precisely shape and finish the given materials with low surface roughness and high surface quality. A grinding machine is a type of machine used to grind workpieces. It basically uses emery or an abrasive wheel as the cutting tool. The grinding process is truly a chip-producing machining process.
List three types of workpiece features that can be produced by using an indexing fixture on the surface grinder. cylindical features, radii, and angles. List three possible solutions to eliminate burn marks on the surface of a workpiece. water-based cutting fluid can greatly reduce heat during grinding, reduce cut depth and/or cross-feed step ...
Cement Grinding Stage. In raw grinding, a ball mill with a high efficiency separator is used to achieve uniform particle size in raw mix for the next stages of the manufacturing process. At the Cement Grinding Stage, 90 – 95% of the clinker is mixed with gypsum and ground in a Cement Ball Mill to produce quality cement OPC 43 and OPC 53.
Grinding Process Grinding is a surface finishing operation where very thin layer of material is removed in the form of dust particles. Thickness of material removed is in range of 0.25 to 0.50 mm. Tool used is a abrasive wheel Grinding machine is a power operated machine tool where, the work piece is fed
It is also known as the Abrasive Grinding Machining Process. Why Abrasive Grinding Machining Process? Because the abrasives are placed on the surface to do the finishing process with much more accuracy. The grinding machine is widely used to finish the workpiece. Do you know why? Because the work removal rate is low between 0.25 …
Set the grinding wheel on the balancing stand and let it settle. The heaviest point of the wheel is now located at the bottom. Weight no. 1 is mounted exactly where the heaviest point of the wheel is and will not be moved. Arrange the two other weights, no. 2 and no. 3, symmetrically at approx. 120°.
This course comprises 18 short working sessions, of 30 - 60 minutes duration each, plus numerous figures and extensive review sessions. Total course duration is equivalent to approximately 15 hours of viewing content. Learning Outcomes. Explain the principles, operation, maintenance and trouble-shooting of grinding units.
Evan Doran. Associate Editor, Modern Machine Shop. On its surface, grinding seems simple: a machine takes a rotating tool (usually a wheel) with abrasive grains and applies it to a workpiece's surface to remove material. Each grain is its own miniature cutting tool, and as grains dull, they tear from the tool and make new, sharp grains …
The machining process is done by the abrasive action of the grinding wheel; the abrasives are embedded over the periphery of the rotating wheel. In Grinding machine grinding …
The grinding process significantly influences the cement's strength development, setting time, and other performance characteristics. The grinding process is a crucial component of the cement production cycle, impacting the organisation operations, productivity, cost efficiency and product quality. Optimal grinding practices, efficient ...
As grinding machines belong to the class of machines for the material removal with geometrically non-defined cutting edges, those machines can be classified in correlation to the classification of the different process technologies with geometrically non-defined cutting edges as it is given in DIN 8589, parts 11, 12, and 13 (DIN 8589-11 …
As a significant milestone, two cement grinding units - Arakkonam Cement Works and Ginigera Cement Works - have transitioned completely to renewable energy from solar and wind. In the process, Arakkonam Cement Works and Ginigera Cement Works achieved a carbon emission savings of 16,500 tonnes (over 6 months …
The measurement of the degree or coarseness of grinding wheel abrasives in which the lower the number, the coarser the wheel; grain sizes range from 8 to 600. Structure The spacing between the individual grains of a grinding wheel, which is identified by the numbers 1 (a dense wheel with the grains close together) through 16 (a very open wheel ...
Figure 2. 1 Power (P) is equal to the product of torque (T) and rotational speed (n): P = T x n. Torque is oficially expressed in Newton x meters (Nm). The oficial SI-unit for rotational speed is radians per second (rad/s). In grinding the accepted term is, however, revolutions per minute (rpm).
These videos and presentations illustrate why one industry expert termed TGS' new centerless grinding machine "a much-needed improvement over other centerless grinders.". The TGS-CL-6020 provides an affordable yet technologically advanced solution to the automotive, aerospace, bearing, fastener, compressor and cutting tool industries.
It is known as a unit process life cycle inventory (UPLCI) [1–4]. As such, this information is reusable in a wide range of products made of di erent materials. Grinding is the first UPLCI in this series, which is in the mass reduction category of the taxonomy of manufactur-ing processes [5–9]. Grinding is an important subtractive machining ...
Cement grinding unit cost. Take the annual output of 600,000 tons of large-scale cement grinding station as an example, there are three common options can be recommended: SCHEME 1: roller press + φ 3.2 ×13m ball mill; SCHEME 2: φ 3.8 ×13m closed mill; SCHEME 3: clinker fine crusher + cement roller press+φ 3.2 ×13m ball mill.
Grinding is an essential process in the manufacture of virtually all types of mechanical equipment and cutting tools. For example, the production of rolling element bearings, automotive components, power generation equipment, and computer and electronic components is critically dependent on grinding processes.
Unlock the full potential of your cement manufacturing process with Zenith's cutting-edge clinker grinding unit and crusher. Learn how to optimize efficiency, improve product quality, and achieve sustainable cement production.
It is an effective machining process for finishing and completing metal parts with tight tolerances. Precision grinding services create a workable solution for tight tolerances and finishing problems that most metal and non-metal manufacturers face. It provides manufacturers with a higher possibility of producing parts without compromising ...
Precision grinding is a machining process that involves a specialist spinning consisting of abrasive particles. These abrasives aid in the removal of some materials …
2022.11.28. Grinding in manufacturing is abrasive machining that is used to finish workpieces, understanding what the grinding process is, how it works, as well as common types of grinding. What is Grinding Process? …
The best method to discover how to optimize the grinding process is called the systems process. This process involves focusing on a few specific factors from each of the four workplace categories and …
حقوق النشر © 2024.Artom كل الحقوق محفوظة.خريطة الموقع