Data mining techniques to assess the condition of …
A new CIGRE SC15 Task Force, 'Data Mining of HV Plant Operation and Condition Monitoring Data'. was established in 2001 to address the activity areas of Study Committee 15, 'Materials for ...
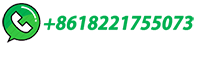
A new CIGRE SC15 Task Force, 'Data Mining of HV Plant Operation and Condition Monitoring Data'. was established in 2001 to address the activity areas of Study Committee 15, 'Materials for ...
RigQuip's condition monitoring and diagnosis system is an asset management tool that keeps watch over your drilling equipment, maximising performance and up time. Unique monitoring technologies and high-performance digital hardware are combined to ensure the earliest possible warning of deteriorating condition in critical assets.
Mine operators also rely on sensors and detection equipment to monitor the condition of mining infrastructure, the environment and equipment, as well as avoid downtimes and operational hazards. ... Mining Technology has listed leading suppliers of sensor-based detection and monitoring equipment and solutions for mining applications, based on ...
Some of the components of a mining condition monitoring system include: • Vibration sensors to detect changes in motors, conveyors, gear boxes and any rotating machinery. • Pressure sensors with temperature compensated output, alongside PT100 temperature sensors. • On-board toxic gas detection modules, as well as flow sensors to …
Introduction. Machine Condition Monitoring (CM) is a vital tool for ensuring high asset reliability and plant availability in the ongoing revolution of modern plant maintenance strategies. However, the mining industry has lagged in the uptake of this methodol-ogy.
Dec 1991. Min Sci Tech. A BASU. Li Yuejin. R.N. Singh. Request PDF | Maintenance strategy for longwall equipment - A condition monitoring approach | Longwall coal mining is a capital-intensive ...
Condition Monitoring to Ensure Reliability for Critical Grinding Equipment in Mining Today's mining operations must keep crucial milling assets online and running optimally, but variations in ore particle size, feed rate …
One of the most compelling reasons to embrace remote wireless condition monitoring in mining is the substantial reduction in site visits. This translates to a significantly lower risk to your team through: ... This reduction includes expenses related to labour, transportation and equipment. Minimal Maintenance Requirements: remote …
Solution: Condition monitoring system on critical equipment. Process: 1. Condition monitoring insights provide operator alerts of potential failures. 2. Proactive scheduling of repairs moves resolution to occur during planned maintenance, partial outage periods or normal equipment rotations. 3.
Aspen Mtell® is an application that uses machine learning to monitor and analyze data across the entirety of the process, from any equipment or system in real-time to detect …
The FOS-based mine hazard detection system offers unique advantages of intrinsic safety, multi-location and multi-parameter monitoring. The application of FOS on monitoring of methane, coal combustion, micro-seismic and equipment condition are described, future trend of research in this area is also discussed.
equipment repairs and sometime serious or even fatal injuries. Fortunately, advances in mining machine condition monitoring are ushering in a new era of productivity, profitability and peace of mind. "Mobile mine equipment represents huge capital costs – it is expensive to operate, expensive to maintain and critically important to mine
Condition monitoring explained. THERE S more to maintenance underground than roller greasing, bit changes and fixing belt splices. Western-based Monitek takes it to a completely new level through its specialization in condition monitoring utilizing vibration monitoring and oil and grease analysis. Donna Schmidt. …
Where the pre-COVID norm was for almost all monitoring to be site-based, more and more mining companies are now swiftly adapting and looking to use their technology and data offsite to drive meaningful change onsite. With emerging trends in the mobile equipment condition monitoring space, it seems like this new way of working is …
Condition Monitoring Opportunity Areas for Mining, Minerals & Metals. Shovel Monitoring. Conveyer Monitoring. SAG / Ball Mill Monitoring. High Pressure Roll …
In order to accurately detect developing failures, condition monitoring requires sophisticated analysis on a reliable source of information-rich data. There are five major technologies, categorized by data source: lubricants, vibrations, stress waves, temperature and electrical signals.
Condition Monitoring to Ensure Reliability for Critical Grinding Equipment in Mining Today's mining operations must keep crucial milling assets online and running optimally, but variations in ore particle size, feed rate and moisture content, can lead to plugging, high vibration and machine bearing wear, and ultimately unscheduled stoppages ...
Multotec supplies a range of condition monitoring products: Hawkeye™ condition monitoring web-based software: Indicates where design changes can be made to extend the life of the component. Prompts inspections. Reduces chances of unplanned stoppages. Simple item display and mine stock codes enables easy ordering. MultoScan laser …
6. MONITORING AND DIAGNOSIS OF MACHINES IN LONGWALL MINING TO UNDERGROUND HARD COAL PRODUCTION For monitoring and diagnosis of machines in longwall mining areas a different measurement concept has to be used like that in open pit mining. The sensor equipment in the longwall mining area must be …
ZHANG Yue-chao. For the special working condition of equipment under coal mine, taken common fault appeared in major mechanical and electrical equipment of Datong Coal Mine Group as example ...
via hardwiring. If wireless is employed, the condition monitoring system is hardwired to the base station, typically via a digital data link. Condition Monitoring System Details The condition monitoring system has two main components: input cards installed in a chassis and one or more PCs running the con-dition monitoring software.
Mining Equipment Monitoring & Protection Solutions Sensors approved for hazardous locations, underground mining, corrosive and high temperature areas Mining operation involves a variety of heavy rotating machinery that is used for exploration and processing of precious metals, minerals and materials extracted from the earth.
Monitoring heavy equipment in mining keeps it in prime condition for efficient operation. Predictive maintenance, a data-driven technique, helps mining engineers anticipate errors before they occur. While traditional maintenance is still necessary for day-to-day operations, predictive maintenance use is increasing.
Remote equipment monitoring is an evolving technology across the Mining industry and our Condition Monitoring Team members are partnering with our customers in innovative ways to improve Finning's ability to improve mechanical availability and reduce equipment total cost of ownership.
Enhanced safety. Reduced human exposure to danger: by deploying sensors in hazardous areas or automating tasks miners can be kept away from potentially risky situations. This includes monitoring for rockfalls, gas leaks and other environmental hazards. Improved situational awareness: real-time data from sensors allows for better …
Our oil condition monitoring sensors are built for earthmoving equipment and fixed plant equipment. Save time and money with Oil Advantage. Contact Us 1-800-872-6160. ... it can go up to 30%. Underground …
An integrated condition monitoring system delivers a scalable and customisable solution for mining operations, enabling plant managers to identify the earliest signs of mechanical failure so that prompt remedial action can be taken. With origins in the mid-nineteenth century, condition monitoring (CM) has become the failsafe solution for …
to find a reliable mining equipment monitoring solution and implement a true Predictive Maintenance program. A Radical Recommendation Fortunately, MSHA (US Mine Safety …
Condition monitoring inspections and automated monitoring with fixed thermal imaging cameras allow mining companies to catch problems in their early stages—before equipment is compromised or destroyed and …
Condition monitoring more than any other maintenance tactic can optimise your maintenance strategy whether you take an online, offline or intime condition monitoring approach. With mining in ...
حقوق النشر © 2024.Artom كل الحقوق محفوظة.خريطة الموقع