Cameco U101
Fuel manufacturing is the last stage of processing before uranium fuel is ready for use in a reactor. The process begins by pressing either natural or enriched UO 2 powder into small cylindrical shapes, measuring about 10 - 13 millimeters in length and 8 - 13.5 millimeters in diameter. These pellets are then baked at a high temperature (1600 – 1700°C), where …
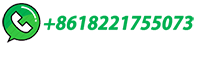