Precision Grinding: Understanding the Principle, Types, and …
It is an effective machining process for finishing and completing metal parts with tight tolerances. Precision grinding services create a workable solution for tight …
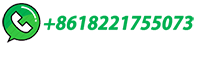
It is an effective machining process for finishing and completing metal parts with tight tolerances. Precision grinding services create a workable solution for tight …
The chosen focus is to understand what are the main research challenges in the extensive industrial use of the process. Since the automotive applications are the most important driving forces for grinding development, the paper starts with an analysis on the main trends in more efficient engines and the changes in their components that will ...
Other articles where grinding is discussed: abrasive: Grinding: Grinding, the most important abrasive application, is in some way involved in the manufacture of almost every product. This use may be direct, as when the product requires pieces that must be made within close dimensional tolerance limits, or a very smooth surface, or…
CNC grinding is a type of CNC machining operation that involves the use of a rotating grinding wheel to remove material from a workpiece, achieving a high degree of precision and surface quality. This automated process is controlled by a CNC ( Computer Numerical Control) system, ensuring accuracy and repeatability in machining tasks.
Precision grinding is a form of grinding process that focuses on manufacturing and finishing parts with very close tolerances. Typically, grinding machining constitutes a subset of cutting as a metal-cutting process in manufacturing and tool-making. In production, grinding is used for machining various materials, particularly for making …
(6) Lapping efficiency is low. The lapping tool material is typically soft and prone to wear, so it should be maintained regularly to ensure its accuracy.. 2. Machinable materials and surfaces of lapping. Grinding can process a variety of metal materials, including steel (including quenched steel), cast iron, copper, and cemented carbide, as …
In Electrochemical grinding, the metal bonded grinding wheel filled with a non-conductive abrasive. The grinding wheel act as a cathode and the workpiece is act as an anode. The electrolyte, which is usually sodium nitrate, sodium chloride, potassium nitrite, with a concentration of 0.150 to 0.300 kg/litre of water.
Concrete is a combination of cement, sand or other fine aggregates, and a coarse aggregate ranging in size from 19 to 25 mm. People use concrete in a wide range of construction applications. Some applications of the different types of cement include: Plastering, masonry construction, pointing, and other purposes.
Industrial grinding operations remove excess or unwanted material from a part. In most grinding applications, the grinding machine is stationary, and the part or workpiece is moved, touching the grinding surface at …
Surface grinding is a type of precision grinding that is used to create flat surfaces on metal workpieces. This process involves using a grinding wheel to remove tiny bits of material from the surface of the workpiece until it is smooth and flat. Surface grinding is an essential process in many metalworking industries, including aerospace ...
Grinding, a term synonymous with precision and efficiency in material removal, stands at the forefront of modern manufacturing techniques. This article …
A grinding machine, often known as a grinder, is a machine tool used for grinding. It is a powerhouse of precision and versatility in the manufacturing and metalworking industry. A grinding machine employs an abrasive wheel as its primary cutting tool for finishing metal and non-metal workpieces.
Preserves product quality: A primary advantage of using cryogenic grinding is it reduces the product size to the required measures without affecting the quality. This is important across various industries, especially food and aquatic products. The process prevents thermal degradation throughout, thereby retaining the needed standard.
Grinding machines come in many types, from light and portable to large and precise. Each has unique applications, costs, and power ratings. Manually operated grinding machines are used for low-precision cutting, cleaning, sharpening, and polishing work while large CNC-operated precision grinders are used to create perfectly flat or …
Abstract. Grinding is a manufacturing process which signi ficantly contributes in producing high precision and durable components. required in numerous applications such as aerospace, defence and ...
Despite the wide industrial application of this process, only a few scientific analyses exist. The science-based analysis of the generating gear grinding needs a high amount of time and effort. One reason is the complex contact conditions between the tool and gear flank, which change continuously during the grinding process.
Grinding is a manufacturing process which significantly contributes in producing high precision and durable components required in numerous applications such as aerospace, defence and automobiles. This review article is focused to uncover history, witness the present and predict the future of the grinding process.
In metal works, Grinding is the metal removal process by the application of abrasives which are bonded to form a rotating wheel. In this grinding process, the metal is removed from the workpiece when the rotating wheel (abrasive) comes in contact with the workpiece. Many of us misunderstood that in this grinding process the metal is …
In the surface grinding process, the grinding wheel revolves on a spindle; and the workpiece, mounted on either a reciprocating or a rotary table, is brought into …
A surface grinder is a machine tool used to provide precision ground surfaces, either to a critical size or for the surface finish. The typical precision of a surface grinder depends on the type and usage, however ±0.002 mm (±0.0001 in) should be achievable on most surface grinders. The machine consists of a table that traverses both ...
Face grinding techniques Approaching to every grinding process begins by stablishing the main geometrical parameters as well as describing the parts involved on the grinding process and defining the movement of these. Once the basic kinematic parameters are set, forces, power and temperatures can be analysed.
Corn Grain Quality for Dry-Milling. A critical initial step in modern industrialization of corn is securing and monitoring the quality of the grain with the purpose of achieving and maintaining efficiencies, effectiveness, and competitiveness. Selected grain quality properties for dry-milling are shown in Table 15.2.
Grinding is a manufacturing process which significantly contributes in producing high precision and durable components required in numerous applications such as...
There are many types of industrial brushes. Examples include: An abrasive brush is used for light deburring, metal finishing, cleaning rust, oxides, defuzzing wood panels, and denibbing plastic. This type of industrial brush will not snag on cut metal edges. An abrasive brush contains an abrasive grit encapsulated into an extruded nylon filament.
See more on mmsonline
WEBAbstract. Grinding is a manufacturing process which significantly contributes in producing high precision and durable components required in …
When Glazing occurs then a single point tipped tool will be used to remove the worn out abrasives from the grinding wheel. This process provides a new and fresh layer of abrasives for removal of material. This process is known as Dressing of grinding wheel and the whole process takes 15 to 20 minutes to operate.
The following uses or applications of Electrochemical Grinding are: ECG is used for grinding turbine blades. It is used in aerospace industries for grinding honeycomb. Also used for finishing hard surfaces. It is also used for creating sharp objects. It is also used for grinding fragile articles. Advantages of Electrochemical Grinding: The ...
A grinding machine is a production machine tool used in the manufacturing industry in which the grinding wheel is attached in the tool post and the workpiece is fixed to the work table and when the operation starts it removes the unwanted material to get the desired surface finish, correct size, and accurate shape of the workpiece.
By Team Xometry. October 18, 2023. 17 min read. Grinding machines are versatile tools used in various industries for material removal, shaping, and finishing. This article explores the definition, uses, types, and practical applications of grinding machines in …
Begin the graining process on a stainless steel weld with a pregrind using a pneumatic right-angle grinder with a plastic support plate with a cooling effect and an 80 grit fiber disc. Finish with a pneumatic drum using a straight grinder. Grain the surface using a right-angle grinder with nonwoven, medium, or high hardness finishing discs.
حقوق النشر © 2024.Artom كل الحقوق محفوظة.خريطة الموقع