Study on the Adsorption Behavior of Polymeric …
For effective grinding, the type and amount of dispersant, the parameters of the grinding process (e.g., grinding machine type, grinding time, grinding machine …
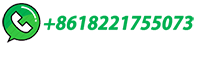
For effective grinding, the type and amount of dispersant, the parameters of the grinding process (e.g., grinding machine type, grinding time, grinding machine …
Wet ultra-fine grinding of a limestone powder (< 100 μm) has been investigated in a stirred media mill with respect to the effect of slurry rheology.The grinding results obtained by various parameters (i.e., molecular weight of a dispersant, solids concentration, additive dosage, addition method and beads load) are evaluated in terms …
The most energy efficient nano grinding was obtained when the smallest grinding media size (90 μm) and stirrer tip speed of 9 m/s were used. ... The dispersant with a low PDI reduced the ...
Lubrizol offers a robust portfolio of high performing dispersant technology and chemistries for a wide range of ink and coating systems to deliver a diverse set of performance requirements and meet broad formulation needs. These systems include aqueous dispersants, non-aqueous dispersants, dispersants, plastic and composite …
THIS PRESENTATION WILL COVER: What is milling? What is media? What do I need to consider when selecting media? What types of media are available? What size, shape, …
By using the optimum dosage of this dispersant, it was possible to run the grinding mill at a higher solids content than without any dispersant present. An upper …
Compared with the curves in Figure 2, the original sample particles of commercial O31 were mostly distributed around 1 μm. After the grinding of the filter cake, the distribution curve was inclined in the …
The dispersant PSIA 1 used in ultrafine grinding has a suitable viscosity of the suspension and generates more hydrogen bonds on the particle surface, and sulfonic acid group in the dispersant PSIA 1 can provide a greater charge density than carboxylic acid groups in the dispersant PAI. In addition, the total potential energies between the ...
All samples were made in 8-ounce glass jars with 100 g of material to work with. Glass beads of size 2.4-2.9 mm were added as grinding media in a 1:1 ratio. The formulations were processed on a Skandex shaker for one hour. After dispersing was completed, samples were cooled to room temperature and filtered through a mesh cone …
When the synthetic grinding dispersant was used in the ultrafine wet grinding of GCC, the fluidity of the GCC slurry was remarkably enhanced. ... 6.1 g/mL were used as the grinding media in the ...
High-speed dispersers are mechanically simple, easy to operate and formulate for. Cycle times for pigment dispersion are typically 30 to 60 min., followed by a 15- to 30-min. letdown. With short cycle times, these dispersers are well suited for the rapid production of paint based on inorganic pigments.
as o/o by weight dry dispersant/dry mineral material. 2-3 Grinding mill and studies A stirred ball grinding mill, manufactured by Drais werke , Germany, was employed for the grind ing tests. A diagrammatic representation of the mill in continuous mode is shown in Figure 2. The grind
The use of electroacoustics as a method for determining the optimum dispersant dosage for the ultrafine grinding of limestone is presented. The technique measures the zeta potential of concentrated suspensions, hence it was possible to study the adsorption of three commercially available polyelectrolyte dispersants onto the …
Using a higher specific weight grinding media is likely to reduce the bead size without losing milling energy by use of equal bead filling volumes. ... and low moisture sensitivity. In aqueous media, the polymeric dispersant can build polymeric shell around the UMP particles and increase the surface charge on the UMP particles, so that the …
Compared with the grinding pigment without any dispersants, grinding with a dispersant resulted in reduced particle size and narrow particle size distribution. In addition, St-HO-PEG-MA2000 exhibited optimal stabilization with a narrow size distribution, small particle size, and particle stability during storage and centrifugation.
The pigment dispersion process involves replacing air-solid interfaces in the dry powder with liquid-solid interfaces and separating the clumps of pigment particles so that they are dispersed in the liquid. The dispersed particles must be separated, or they will flocculate to form new clumps. The dispersant may be a polymer solution (possibly ...
While grinding media may govern a number of chemical reactions during grinding, the formation of iron hydroxides has a significant effect on mineral flotation (Grano, 2009). ... clay ores after grinding with different grinding media was performed to understand the interaction of lignosulfonate dispersant and grinding conditions …
What Are The Key Functions Of Dispersing Agents? Dispersing agents, also known as dispersants or dispersing aids, serve several essential functions in …
Grinding media degradation was analyzed by comprehensive shape analyses. ... 2.7 μm was produced with a corresponding SE input of 270 kWh/ton using silica beads ranging from 420 to 850 μm and a dispersant dosage of 14 kg/ton. Moreover, the mathematical models generated based on population balance modeling provided an …
The process of dispersion is done to get as close as possible to the primary particle's original size, which improves the application process and provides better end …
In its market sector, the "Grinding & Dispersing" Business Unit of the NETZSCH Group has been a market leader for decades – and that goes for everything from laboratory-scale machines to production plants. The …
g alumina grinding media and milled for 30 minutes. Recommended Use Levels (mg D-3005/m2 surface area) The recommended use level of a dispersant is a function of powder surface area, not powder weight. For this reason, recommended use levels are given in …
A polymeric dispersant called Dispersant S40 with a molecular weight of 5500 gives the best grinding results. For a certain level of beads load, an optimal solids concentration exists.
11. 1 Introduction. The process of dispersion includes grinding and distri-bution of pigment particles evenly into a medium. The maximum colorimetric properties can only be …
The results indicate that the D 50 particle size of the vitrified bond powder is refined to 0.186 μm by employing smaller size (5 mm) of the grinding media, 2.5%(mass fraction) dispersant addition and 2 hours milling time. Meanwhile, the dispersion of the particle is good and there is no agglomeration after ball milling.
Discover a range of high-performance steel ball sizes meticulously crafted by Inathi Grinding Media. Our product lineup includes precision-engineered options such as 70mm, 60mm, 40mm, and 30-35mm 12% Cr Steel Balls. Rigorously tested in independent laboratories, our products guarantee consistent, superior performance in even the most …
The grinding media were yttrium-stabilized zirconia beads with a size of 0.2–0.3 mm, setting its volume filling rate to 80 vol.%. The various dispersants (i.e., PASH and PMASH S) at different adding amounts (i.e., 1 wt.%, 3 wt.% and 5 wt.%) were used in ultrafine grinding of CoAl 2 O 4 particles. The grinding time is 30, 60, 90 and 120 min ...
Grinding media. Clay ores. Copper and gold flotation. Lignosulfonate dispersant. 1. Introduction. In mineral processing, hydrophilic alumino-silicate clay …
The grinding media used were yttrium-stabilized zirconia beads with the sizes of 0.3–0.5 mm, and its volume filling rate was 75 vol.%. The dispersants PD0x (PD01, PD02, and PD03) in different amounts were used in grinding of S-ZnF particle raw materials. ... By adding 2 wt.% dispersant PD02 to the grinding process of the S-ZnF …
During ultra-fine grinding in stirred media mills, the typical maximum percentage solids by weight in a slurry is approximately 50% without dispersant, whereas an upper limitation of solids concentration is up to 80 wt.% in the presence of an optimal dispersant [13].
حقوق النشر © 2024.Artom كل الحقوق محفوظة.خريطة الموقع